Tendência mundial, áreas portuárias desativadas viram praias de concreto
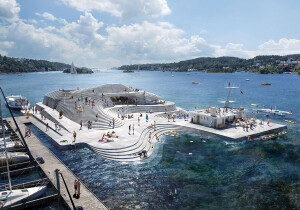
Crédito: Snøhetta
Em Arendal, na Noruega, o porto desativado da cidade será transformado em uma praia artificial de concreto. O projeto arquitetônico é do reconhecido escritório norueguês Snøhetta. A obra está prevista para ser inaugurada em 2024 e segue tendência mundial de reurbanização de áreas portuárias, transformando-as em parques, áreas de gastronomia, locais para a prática de esportes, praias e ilhas artificiais.
A Snøhetta, em parceria com empreiteiros, pesquisadores e a indústria de concreto da Noruega, vai utilizar no projeto em Arendal pré-fabricados com emissão negativa de CO₂. Como isso será possível? Os painéis-sanduíche que serão usados na obra são projetados com concreto autoadensável e preenchidos com biomassa gerada através das cascas das árvores usadas pela indústria de madeira do país – também conhecida como biochar. “São paredes que fazem o aproveitamento de restos das madeireiras misturadas a um concreto leve”, explica Alexandra Roos Rassat, gerente de projeto da Norwegian Biochar Network.
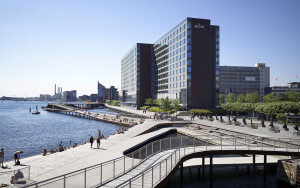
Crédito: Julien De Smedt
Na Noruega, a maioria desses resíduos de madeira é incinerada pela indústria, gerando grande emissão de CO₂. Com a transformação em biomassa e a aplicação no preenchimento dos painéis-sanduíche, a Snøhetta acredita ter encontrado uma solução para continuar utilizando concreto em seus projetos sem elevar a emissão de CO₂. “É difícil imaginar que encontraremos um substituto para um material tão versátil como o concreto. Então, temos que buscar alternativas para seguir construindo sem estourar as metas de emissão de CO₂”, diz Carsten Løddesøl, gerente de projeto da Snøhetta.
Todas as construções inovadoras têm o concreto como elemento transformador
Em Copenhague, na Dinamarca, os moradores e turistas já usufruem de uma praia de concreto construída após a desativação do porto nos anos 1980. É o Kalvebod Waves, inaugurado em 2013 e projetado pelo escritório dinamarquês Julien De Smedt. A ideia consiste em um vasto píer em concreto, com elevações que transmitem ao público a sensação de que ele caminha sobre ondas. O local é um dos mais visitados em Copenhague durante o verão.
Na cidade de Nova York, nos Estados Unidos, foi inaugurada em maio de 2021 a Little Island. Trata-se de uma ilha de concreto que faz parte do complexo de obras para revitalizar a região portuária à beira do rio Hudson. A estrutura se sustenta sobre grandes tulipas de concreto pré-fabricado e a abertura do parque coincidiu com a vacinação em massa da população de NY. Resultado: transformou-se no local mais visitado na cidade durante o verão.
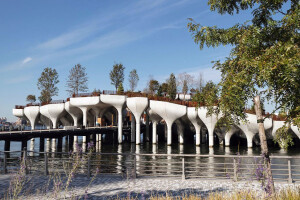
Crédito: Little Island
Os projetos são variados, como mostram as transformações bem-sucedidas ocorridas em Barcelona-Espanha, Buenos Aires-Argentina, Gênova-Itália e Cidade do Cabo-África do Sul. Há também os exemplos brasileiros do Rio de Janeiro-RJ, de Porto Alegre-RS e de Belém-PA. Todos têm em comum o concreto como elemento transformador, como define o professor-doutor Paulo Helene. “O concreto criou a arte de projetar e construir estruturas. As obras, antes limitadas à alvenaria estrutural, ganharam novas alternativas e inúmeras possibilidades”, afirma.
Entrevistado
Escritórios de arquitetura Snøhetta, Julien De Smedt e Little Island
Contatos
contact@snohetta.com
office@jdsa.eu
info@littleisland.org
Jornalista responsável:
Altair Santos MTB 2330
Tendência mundial, áreas portuárias desativadas viram praias de concreto
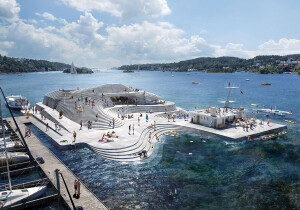
Crédito: Snøhetta
Em Arendal, na Noruega, o porto desativado da cidade será transformado em uma praia artificial de concreto. O projeto arquitetônico é do reconhecido escritório norueguês Snøhetta. A obra está prevista para ser inaugurada em 2024 e segue tendência mundial de reurbanização de áreas portuárias, transformando-as em parques, áreas de gastronomia, locais para a prática de esportes, praias e ilhas artificiais.
A Snøhetta, em parceria com empreiteiros, pesquisadores e a indústria de concreto da Noruega, vai utilizar no projeto em Arendal pré-fabricados com emissão negativa de CO₂. Como isso será possível? Os painéis-sanduíche que serão usados na obra são projetados com concreto autoadensável e preenchidos com biomassa gerada através das cascas das árvores usadas pela indústria de madeira do país – também conhecida como biochar. “São paredes que fazem o aproveitamento de restos das madeireiras misturadas a um concreto leve”, explica Alexandra Roos Rassat, gerente de projeto da Norwegian Biochar Network.
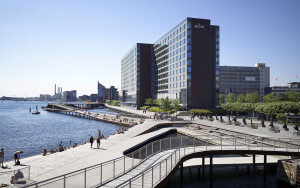
Crédito: Julien De Smedt
Na Noruega, a maioria desses resíduos de madeira é incinerada pela indústria, gerando grande emissão de CO₂. Com a transformação em biomassa e a aplicação no preenchimento dos painéis-sanduíche, a Snøhetta acredita ter encontrado uma solução para continuar utilizando concreto em seus projetos sem elevar a emissão de CO₂. “É difícil imaginar que encontraremos um substituto para um material tão versátil como o concreto. Então, temos que buscar alternativas para seguir construindo sem estourar as metas de emissão de CO₂”, diz Carsten Løddesøl, gerente de projeto da Snøhetta.
Todas as construções inovadoras têm o concreto como elemento transformador
Em Copenhague, na Dinamarca, os moradores e turistas já usufruem de uma praia de concreto construída após a desativação do porto nos anos 1980. É o Kalvebod Waves, inaugurado em 2013 e projetado pelo escritório dinamarquês Julien De Smedt. A ideia consiste em um vasto píer em concreto, com elevações que transmitem ao público a sensação de que ele caminha sobre ondas. O local é um dos mais visitados em Copenhague durante o verão.
Na cidade de Nova York, nos Estados Unidos, foi inaugurada em maio de 2021 a Little Island. Trata-se de uma ilha de concreto que faz parte do complexo de obras para revitalizar a região portuária à beira do rio Hudson. A estrutura se sustenta sobre grandes tulipas de concreto pré-fabricado e a abertura do parque coincidiu com a vacinação em massa da população de NY. Resultado: transformou-se no local mais visitado na cidade durante o verão.
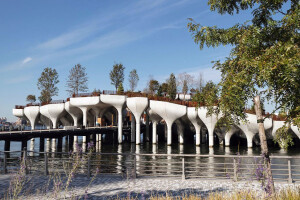
Crédito: Little Island
Os projetos são variados, como mostram as transformações bem-sucedidas ocorridas em Barcelona-Espanha, Buenos Aires-Argentina, Gênova-Itália e Cidade do Cabo-África do Sul. Há também os exemplos brasileiros do Rio de Janeiro-RJ, de Porto Alegre-RS e de Belém-PA. Todos têm em comum o concreto como elemento transformador, como define o professor-doutor Paulo Helene. “O concreto criou a arte de projetar e construir estruturas. As obras, antes limitadas à alvenaria estrutural, ganharam novas alternativas e inúmeras possibilidades”, afirma.
Entrevistado
Escritórios de arquitetura Snøhetta, Julien De Smedt e Little Island
Contatos
contact@snohetta.com
office@jdsa.eu
info@littleisland.org
Jornalista responsável:
Altair Santos MTB 2330
Conheça o 1º estádio do Brasil construído com tecnologia BIM
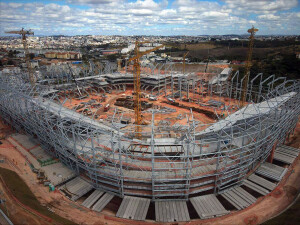
Crédito: Arena MRV
Com capacidade para 46.000 lugares, a Arena do Galo é o primeiro estádio brasileiro construído 100% com o emprego da tecnologia BIM (Modelo de Informação da Construção). As partes estrutural, arquitetônica e de instalações foram digitalmente projetadas antes de serem viabilizadas no canteiro de obras. Até que começasse a execução, por 2 anos o projeto do estádio foi submetido aos softwares em BIM para que todas as possibilidades de interferência pudessem ser analisadas e corrigidas.
Segundo o gerente de projetos da obra, o engenheiro civil Diego Fernandes Pontes, o uso do BIM permitiu identificar os ajustes necessários nos projetos de estrutura, arquitetura e de instalações hidráulicas e elétricas, eliminando problemas que, usualmente, são detectados durante a execução. Isso tem permitido que o cronograma de construção do estádio esteja em dia. O prazo é de 30 meses e a entrega da obra está mantida para outubro de 2022. A fase de execução começou em abril de 2020.
A arena do Atlético Mineiro está em construção em Belo Horizonte-MG e terá 180 mil m² de área construída. O volume de concreto envolve 38.000 m³ de material pré-fabricado e 46.000 m³ de estruturas moldadas in loco, além de 7.400 toneladas de aço em vergalhão e cordoalha e 4.000 toneladas de estruturas metálicas. O custo da obra de 560 milhões de reais segue mantido e, segundo Diego Fernandes, muito em função da adoção do BIM. “Um projeto dessa amplitude só tem a ganhar com a tecnologia. Em todos os aspectos: planejamento, segurança técnica, construtivo, custo, ambiental e prazo de execução”, diz.
Indiretamente, construção induz a geração de 13 mil postos de trabalho
O projeto da Arena do Galo utiliza a versão BIM 6D, que está vinculada à eficiência energética, pegada de carbono, manutenção e operação do estádio em seu período de vida útil. A tecnologia, juntamente com o emprego da construção industrializada, também resultou em um canteiro de obras mais enxuto. No pico da obra, mil trabalhadores atuam na construção do estádio. No entanto, segundo o SindusCon-MG, houve um incremento na geração de empregos na cadeia produtiva da construção civil local, já que foi dada prioridade para fornecedores de Belo Horizonte e do entorno da capital mineira. Segundo o sindicato, o estádio induz a geração de 13 mil postos de trabalho.
Outra inovação que envolve a Arena do Galo é que se trata do primeiro estádio brasileiro a passar por um ensaio de túnel de vento. O teste foi realizado em Londres-Inglaterra, pela BMT Fluid Mechanics. A verificação das pressões e esforços de vento permitiu otimizar o projeto estrutural da obra. A maquete estrutural incluiu a topografia do local e os prédios e residências no entorno do estádio, para que a obra não causasse danos nas construções vizinhas. A mesma empresa que promoveu o ensaio de túnel de vento foi também a que avaliou arenas recentemente construídas na Inglaterra, como New Anfield, Emirates Stadium e Old Trafford.
De acordo com o gerente de projetos da obra, o engenheiro civil Diego Fernandes Pontes, projetos em BIM envolvem uma grande gama de disciplinas e exigem sintonia entre os projetistas. “Isso demanda uma coordenação muito eficaz, para que se possa usufruir ao máximo da tecnologia”, completa.
Veja a palestra do engenheiro civil Diego Fernandes Pontes (entre 1h05min e 1h37min do vídeo)
Entrevistado
Reportagem com base no webinar “Gestão e Metodologia: Case Arena MRV”, promovido pela Câmara Brasileira da Indústria da Construção (CBIC)
Contato
ascom@cbic.org.br
Jornalista responsável:
Altair Santos MTB 2330
Conheça o 1º estádio do Brasil construído com tecnologia BIM
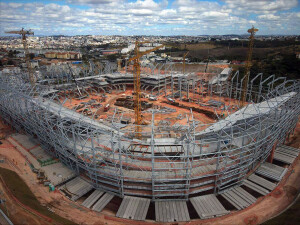
Crédito: Arena MRV
Com capacidade para 46.000 lugares, a Arena do Galo é o primeiro estádio brasileiro construído 100% com o emprego da tecnologia BIM (Modelo de Informação da Construção). As partes estrutural, arquitetônica e de instalações foram digitalmente projetadas antes de serem viabilizadas no canteiro de obras. Até que começasse a execução, por 2 anos o projeto do estádio foi submetido aos softwares em BIM para que todas as possibilidades de interferência pudessem ser analisadas e corrigidas.
Segundo o gerente de projetos da obra, o engenheiro civil Diego Fernandes Pontes, o uso do BIM permitiu identificar os ajustes necessários nos projetos de estrutura, arquitetura e de instalações hidráulicas e elétricas, eliminando problemas que, usualmente, são detectados durante a execução. Isso tem permitido que o cronograma de construção do estádio esteja em dia. O prazo é de 30 meses e a entrega da obra está mantida para outubro de 2022. A fase de execução começou em abril de 2020.
A arena do Atlético Mineiro está em construção em Belo Horizonte-MG e terá 180 mil m² de área construída. O volume de concreto envolve 38.000 m³ de material pré-fabricado e 46.000 m³ de estruturas moldadas in loco, além de 7.400 toneladas de aço em vergalhão e cordoalha e 4.000 toneladas de estruturas metálicas. O custo da obra de 560 milhões de reais segue mantido e, segundo Diego Fernandes, muito em função da adoção do BIM. “Um projeto dessa amplitude só tem a ganhar com a tecnologia. Em todos os aspectos: planejamento, segurança técnica, construtivo, custo, ambiental e prazo de execução”, diz.
Indiretamente, construção induz a geração de 13 mil postos de trabalho
O projeto da Arena do Galo utiliza a versão BIM 6D, que está vinculada à eficiência energética, pegada de carbono, manutenção e operação do estádio em seu período de vida útil. A tecnologia, juntamente com o emprego da construção industrializada, também resultou em um canteiro de obras mais enxuto. No pico da obra, mil trabalhadores atuam na construção do estádio. No entanto, segundo o SindusCon-MG, houve um incremento na geração de empregos na cadeia produtiva da construção civil local, já que foi dada prioridade para fornecedores de Belo Horizonte e do entorno da capital mineira. Segundo o sindicato, o estádio induz a geração de 13 mil postos de trabalho.
Outra inovação que envolve a Arena do Galo é que se trata do primeiro estádio brasileiro a passar por um ensaio de túnel de vento. O teste foi realizado em Londres-Inglaterra, pela BMT Fluid Mechanics. A verificação das pressões e esforços de vento permitiu otimizar o projeto estrutural da obra. A maquete estrutural incluiu a topografia do local e os prédios e residências no entorno do estádio, para que a obra não causasse danos nas construções vizinhas. A mesma empresa que promoveu o ensaio de túnel de vento foi também a que avaliou arenas recentemente construídas na Inglaterra, como New Anfield, Emirates Stadium e Old Trafford.
De acordo com o gerente de projetos da obra, o engenheiro civil Diego Fernandes Pontes, projetos em BIM envolvem uma grande gama de disciplinas e exigem sintonia entre os projetistas. “Isso demanda uma coordenação muito eficaz, para que se possa usufruir ao máximo da tecnologia”, completa.
Veja a palestra do engenheiro civil Diego Fernandes Pontes (entre 1h05min e 1h37min do vídeo)
Entrevistado
Reportagem com base no webinar “Gestão e Metodologia: Case Arena MRV”, promovido pela Câmara Brasileira da Indústria da Construção (CBIC)
Contato
ascom@cbic.org.br
Jornalista responsável:
Altair Santos MTB 2330
Marco do saneamento agrega novas tecnologias de construção ao setor
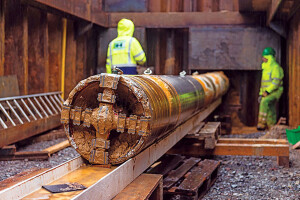
Crédito: Herrenknecht AG
O déficit de tratamento de esgoto, fornecimento de água potável e captação das águas pluviais no Brasil atinge diretamente 100 milhões de pessoas. É praticamente metade da população do país. O Marco Legal do Saneamento, que recentemente completou 1 ano, surgiu para enfrentar esse problema. Ele abre caminho para que o setor privado possa atuar no mercado, suprindo a falta de investimentos e a escassez de projetos das estatais.
Além de injetar recursos, a privatização do saneamento agrega também novas tecnologias. Engenheiros civis e engenheiros sanitaristas que participaram do “7º Fórum de Infraestrutura Grandes Construções: Saneamento – Desafios da Universalização” mostraram quais inovações estão disponíveis para acelerar o ritmo de obras de infraestrutura e também para conter desperdícios como os vazamentos nas tubulações.
No debate, o engenheiro civil Wagner Oliveira de Carvalho, líder do programa Infra Inteligente da Aegea Saneamento, afirma que não dá mais para projetar obras de saneamento sem usar o BIM (Modelo de Informação da Construção). “Essa ferramenta garante um retorno robusto na gestão de ativos. Por isso, precisa ser tratado como um investimento”, diz. O palestrante também mostrou como a Inteligência Artificial traz eficácia à criação de novas redes de abastecimento, acoplada ao uso de drones para gerenciar as obras.
União de saneamento básico com tecnologia torna as cidades mais resilientes
Para Wagner Oliveira de Carvalho, saneamento e tecnologia tornam as cidades mais resilientes. Convicção que foi reforçada pela palestra do engenheiro civil Federico Lagreca, CEO da Suez Water Technologies no Brasil. Ele informa que atualmente existem ferramentas capazes de identificar vazamentos em tubulações, o que gera economia de milhões de dólares. “Vamos supor uma cidade de médio porte com a produção de 380 mil m³ por dia de água potável. Se ela tiver uma perda de 25% em suas tubulações, isso vai gerar 13 milhões de dólares de prejuízo por ano”, alerta.
Federico Lagreca complementa dizendo que o que combate o desperdício é a tecnologia. “O gerenciamento eficaz da rede de distribuição reduz custos operacionais, controla o consumo de água e economiza energia”, garante. Isso também passa pelas inovações que envolvem as tubulações e os projetos de engenharia voltados para o saneamento, como expôs Edson Peev, engenheiro-sênior da Herrenknecht AG. O especialista falou sobre soluções não-destrutivas, como os túneis de esgoto profundo para o transporte e armazenamento dos rejeitos das estações de tratamento.
Esse material fica aprisionado em escavações subterrâneas e é encapsulado por paredes de concreto. A tecnologia empregada se assemelha ao que proporciona a abertura de túneis para o tráfego de metrôs. “Porém, são escavações com diâmetros menores”, explica Edson Peev. O engenheiro civil assegura que o emprego desse sistema gera economia de energia e poupa a construção de novas estações de tratamento. “Em Melbourne, na Austrália, e em Hong Kong, na China, esse modelo já é empregado com sucesso”, finaliza.
Entrevistado
Reportagem com base nas informações trazidas pelo “7º Fórum de Infraestrutura Grandes Construções: Saneamento – Desafios da Universalização”
Contato
sobratema@sobratema.org.br
Jornalista responsável:
Altair Santos MTB 2330
Marco do saneamento agrega novas tecnologias de construção ao setor
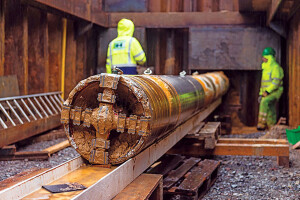
Crédito: Herrenknecht AG
O déficit de tratamento de esgoto, fornecimento de água potável e captação das águas pluviais no Brasil atinge diretamente 100 milhões de pessoas. É praticamente metade da população do país. O Marco Legal do Saneamento, que recentemente completou 1 ano, surgiu para enfrentar esse problema. Ele abre caminho para que o setor privado possa atuar no mercado, suprindo a falta de investimentos e a escassez de projetos das estatais.
Além de injetar recursos, a privatização do saneamento agrega também novas tecnologias. Engenheiros civis e engenheiros sanitaristas que participaram do “7º Fórum de Infraestrutura Grandes Construções: Saneamento – Desafios da Universalização” mostraram quais inovações estão disponíveis para acelerar o ritmo de obras de infraestrutura e também para conter desperdícios como os vazamentos nas tubulações.
No debate, o engenheiro civil Wagner Oliveira de Carvalho, líder do programa Infra Inteligente da Aegea Saneamento, afirma que não dá mais para projetar obras de saneamento sem usar o BIM (Modelo de Informação da Construção). “Essa ferramenta garante um retorno robusto na gestão de ativos. Por isso, precisa ser tratado como um investimento”, diz. O palestrante também mostrou como a Inteligência Artificial traz eficácia à criação de novas redes de abastecimento, acoplada ao uso de drones para gerenciar as obras.
União de saneamento básico com tecnologia torna as cidades mais resilientes
Para Wagner Oliveira de Carvalho, saneamento e tecnologia tornam as cidades mais resilientes. Convicção que foi reforçada pela palestra do engenheiro civil Federico Lagreca, CEO da Suez Water Technologies no Brasil. Ele informa que atualmente existem ferramentas capazes de identificar vazamentos em tubulações, o que gera economia de milhões de dólares. “Vamos supor uma cidade de médio porte com a produção de 380 mil m³ por dia de água potável. Se ela tiver uma perda de 25% em suas tubulações, isso vai gerar 13 milhões de dólares de prejuízo por ano”, alerta.
Federico Lagreca complementa dizendo que o que combate o desperdício é a tecnologia. “O gerenciamento eficaz da rede de distribuição reduz custos operacionais, controla o consumo de água e economiza energia”, garante. Isso também passa pelas inovações que envolvem as tubulações e os projetos de engenharia voltados para o saneamento, como expôs Edson Peev, engenheiro-sênior da Herrenknecht AG. O especialista falou sobre soluções não-destrutivas, como os túneis de esgoto profundo para o transporte e armazenamento dos rejeitos das estações de tratamento.
Esse material fica aprisionado em escavações subterrâneas e é encapsulado por paredes de concreto. A tecnologia empregada se assemelha ao que proporciona a abertura de túneis para o tráfego de metrôs. “Porém, são escavações com diâmetros menores”, explica Edson Peev. O engenheiro civil assegura que o emprego desse sistema gera economia de energia e poupa a construção de novas estações de tratamento. “Em Melbourne, na Austrália, e em Hong Kong, na China, esse modelo já é empregado com sucesso”, finaliza.
Entrevistado
Reportagem com base nas informações trazidas pelo “7º Fórum de Infraestrutura Grandes Construções: Saneamento – Desafios da Universalização”
Contato
sobratema@sobratema.org.br
Jornalista responsável:
Altair Santos MTB 2330
É possível produzir concreto UHPC com resíduos da construção?
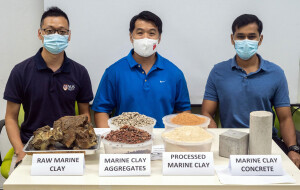
Crédito: National University of Singapore
A escassez de areia em Cingapura fez com que pesquisadores da principal universidade da cidade-estado se concentrassem na busca por insumos alternativos. A solução veio dos resíduos da construção civil. O que a equipe do centro avançado de materiais e estruturas da Universidade Nacional de Cingapura não esperava é que a areia desenvolvida em laboratório cumprisse função semelhante aos aditivos para concretos especiais, como o UHPC (ultra-high performance concreto [concreto de ultra-alta resistência]).
Os pesquisadores descobriram que a areia produzida na universidade estimula os elementos ligantes que geram o UHPC, cuja principal característica é alcançar resistências superiores a 200 MPa. E como se chegou a esse material? Cingapura é um arquipélago de quase 60 ilhas. A escassez de território faz com que os resíduos das construções, assim como restos de escavações de túneis, sejam lançados ao mar para gerar aterros. Com o passar do tempo, esse material se transforma no que o estudo definiu como “argila residual”.
Nos laboratórios da Universidade Nacional de Cingapura, a argila foi dessalinizada, aquecida a 700 °C e misturada com areia de pó de quartzo, gerando uma areia mais fina que a convencional e que possibilita um consumo menor de água para a produção de concreto. A pesquisa começou em 2020, mas segue em fase de aprimoramento. O que a equipe da Universidade Nacional de Cingapura espera é que a areia a partir de resíduos da construção seja capaz de produzir concretos mais duráveis e que emitam menos CO₂.
Pesquisadores têm a expectativa de conseguir reduzir o custo de produção de concretos especiais
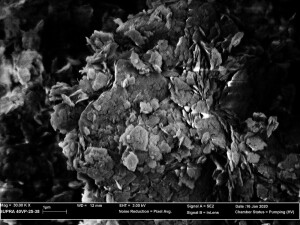
Crédito: National University of Singapore
Em dezembro de 2020, a pesquisa foi publicada no jornal científico Construction and Building Materials. O texto do resumo diz o seguinte: “A argila utilizada no estudo, obtida através de resíduos de escavações em Cingapura, é uma argila caulinita de baixo teor (29%). O material foi seco, moído e calcinado a 700 °C para ativar os aluminatos por meio de desidroxilação. À argila calcinada foram acrescentados 30% da areia de pó de quartzo, resultando em um insumo que contribuiu para melhorar a resistência à compressão do UHPC.”
A pesquisa foi coordenada pelo professor-associado da Universidade Nacional de Cingapura, Pang Sze Dai. Segundo ele, a descoberta abre caminho para transformar os resíduos em recursos minerais. “Esta é a primeira vez que a argila residual de baixa qualidade é usada como insumo de concreto. Globalmente, esse material é abundante e tem potencial para ajudar a diminuir a pegada de carbono e reduzir o custo de produção de concretos especiais”, avalia.
Em fevereiro de 2021, uma versão atualizada da pesquisa foi publicada no Journal of Cleaner Production. O estudo aponta para a possibilidade de se conseguir dessalinizar a água e a areia do mar para utilizá-las na produção de concreto. Atualmente, Cingapura é um dos maiores importadores de areia de rio e de água doce do mundo.
Entrevistado
Centro avançado de materiais e estruturas da Universidade Nacional de Cingapura
Contato
enquiry@nus.edu.sg
Jornalista responsável:
Altair Santos MTB 2330
É possível produzir concreto UHPC com resíduos da construção?
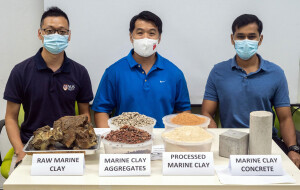
Crédito: National University of Singapore
A escassez de areia em Cingapura fez com que pesquisadores da principal universidade da cidade-estado se concentrassem na busca por insumos alternativos. A solução veio dos resíduos da construção civil. O que a equipe do centro avançado de materiais e estruturas da Universidade Nacional de Cingapura não esperava é que a areia desenvolvida em laboratório cumprisse função semelhante aos aditivos para concretos especiais, como o UHPC (ultra-high performance concreto [concreto de ultra-alta resistência]).
Os pesquisadores descobriram que a areia produzida na universidade estimula os elementos ligantes que geram o UHPC, cuja principal característica é alcançar resistências superiores a 200 MPa. E como se chegou a esse material? Cingapura é um arquipélago de quase 60 ilhas. A escassez de território faz com que os resíduos das construções, assim como restos de escavações de túneis, sejam lançados ao mar para gerar aterros. Com o passar do tempo, esse material se transforma no que o estudo definiu como “argila residual”.
Nos laboratórios da Universidade Nacional de Cingapura, a argila foi dessalinizada, aquecida a 700 °C e misturada com areia de pó de quartzo, gerando uma areia mais fina que a convencional e que possibilita um consumo menor de água para a produção de concreto. A pesquisa começou em 2020, mas segue em fase de aprimoramento. O que a equipe da Universidade Nacional de Cingapura espera é que a areia a partir de resíduos da construção seja capaz de produzir concretos mais duráveis e que emitam menos CO₂.
Pesquisadores têm a expectativa de conseguir reduzir o custo de produção de concretos especiais
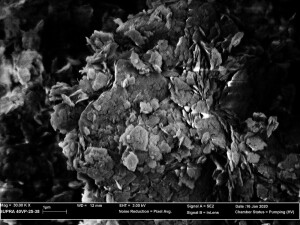
Crédito: National University of Singapore
Em dezembro de 2020, a pesquisa foi publicada no jornal científico Construction and Building Materials. O texto do resumo diz o seguinte: “A argila utilizada no estudo, obtida através de resíduos de escavações em Cingapura, é uma argila caulinita de baixo teor (29%). O material foi seco, moído e calcinado a 700 °C para ativar os aluminatos por meio de desidroxilação. À argila calcinada foram acrescentados 30% da areia de pó de quartzo, resultando em um insumo que contribuiu para melhorar a resistência à compressão do UHPC.”
A pesquisa foi coordenada pelo professor-associado da Universidade Nacional de Cingapura, Pang Sze Dai. Segundo ele, a descoberta abre caminho para transformar os resíduos em recursos minerais. “Esta é a primeira vez que a argila residual de baixa qualidade é usada como insumo de concreto. Globalmente, esse material é abundante e tem potencial para ajudar a diminuir a pegada de carbono e reduzir o custo de produção de concretos especiais”, avalia.
Em fevereiro de 2021, uma versão atualizada da pesquisa foi publicada no Journal of Cleaner Production. O estudo aponta para a possibilidade de se conseguir dessalinizar a água e a areia do mar para utilizá-las na produção de concreto. Atualmente, Cingapura é um dos maiores importadores de areia de rio e de água doce do mundo.
Entrevistado
Centro avançado de materiais e estruturas da Universidade Nacional de Cingapura
Contato
enquiry@nus.edu.sg
Jornalista responsável:
Altair Santos MTB 2330
Alemanha ergue 1ª edificação com concreto de carbono
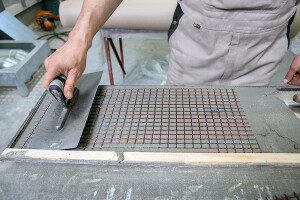
Crédito: Jörg Singer/TU Dresden
Está em construção no campus da Universidade Tecnológica de Dresden, na Alemanha, a primeira edificação que dispensa armaduras de aço, substituindo-as por telas de fios de fibras de carbono. Sai o concreto armado e entra o concreto de carbono, como definem os pesquisadores da TU Dresden.
A vantagem da tela com fios de fibras de carbono é que ela não sofre a ameaça de carbonatação, como ocorre com as armaduras convencionais. Portanto, está isenta de algumas patologias que atingem o concreto armado. Por isso, de acordo com os ensaios em laboratório, o concreto de carbono tende a ter vida útil mais longa.
Outra característica do concreto que usa armadura à base de fibras de carbono é que ele é 4 vezes mais resistente que o concreto convencional. “Isso permite projetar estruturas mais esbeltas, e que conseguem suportar cargas iguais a grandes estruturas de concreto armado”, diz o engenheiro civil e arquiteto Gunter Henn, da Henn Arquitetura, que projetou o edifício em construção na TU Dresden.
O prédio batizado de “The Cube” foi planejado para ter laboratórios e salas de evento. Henn projetou o edifício em parceria com o Instituto de Estruturas de Concreto da TU Dresden. “A meta é que a construção emita 50% menos CO₂ que uma construção convencional”, afirma o professor Manfred Curbach, que atua na universidade alemã.
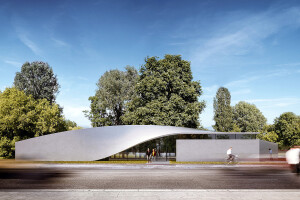
Crédito: Heen
A ideia é que o edifício seja uma vitrine para a pesquisa da TU Dresden chamada de C³ (Composto de Concreto de Carbono). Existe investimento do governo alemão no projeto, que passou a estimular estudos que criem materiais na construção mais sustentáveis. “Além de gerar estruturas com alto desempenho, o concreto de carbono permite desenhos arquitetônicos com mais curvas”, completa Henn.
Custo do concreto de carbono é estimado em 20 vezes mais caro que o concreto convencional
O “The Cube” terá 200 m² de área construída e também contará com paredes de vidro e estruturas de concreto armado nas partes menos desafiadoras da concepção arquitetônica, como o radier e as fundações. O maior volume de C³ será usado na construção de uma das paredes laterais do edifício, que avança para se transformar no teto da obra. Todos os elementos com concreto de carbono serão pré-fabricados. O prédio já se encontra em fase de execução e a previsão é que seja inaugurado no 1º semestre de 2022.
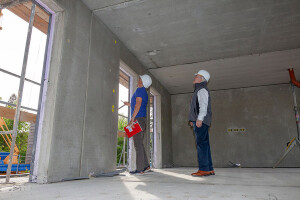
Crédito: Stefan Gröschel/TU Dresden
O custo do concreto de carbono é estimado em 20 vezes mais caro que o concreto armado convencional. “A redução de custos ocorrerá no futuro, à medida que as técnicas de adição de fibra de carbono ao concreto forem aprimoradas”, avalia Manfred Curbach. A construção do “The Cube” está estimada em 5 milhões de euros.
O concreto que usa armadura à base de fibras de carbono está em pesquisa na Alemanha desde 2008. Dentro do país, mais de 140 institutos de pesquisa, empresas de construção e instituições públicas estão envolvidos no estudo. O Ministério Federal da Educação e Pesquisa financia o trabalho interdisciplinar com um orçamento de 45 milhões de euros.
Também está em estudo na Alemanha o uso do concreto de carbono para restaurar pontes que estejam perto de completar 50 anos de vida útil. Estima-se que o material permita construir estruturas que suportem até 80 anos sem exigir manutenção.
Entrevistado
Escritório de arquitetura Henn e Instituto de Estruturas de Concreto da Universidade Tecnológica de Dresden
Contatos
info@henn.com
pressestelle@tu-dresden.de
Jornalista responsável:
Altair Santos MTB 2330
Alemanha ergue 1ª edificação com concreto de carbono
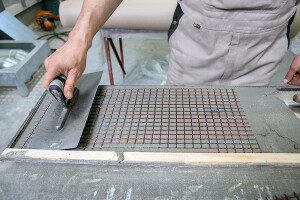
Crédito: Jörg Singer/TU Dresden
Está em construção no campus da Universidade Tecnológica de Dresden, na Alemanha, a primeira edificação que dispensa armaduras de aço, substituindo-as por telas de fios de fibras de carbono. Sai o concreto armado e entra o concreto de carbono, como definem os pesquisadores da TU Dresden.
A vantagem da tela com fios de fibras de carbono é que ela não sofre a ameaça de carbonatação, como ocorre com as armaduras convencionais. Portanto, está isenta de algumas patologias que atingem o concreto armado. Por isso, de acordo com os ensaios em laboratório, o concreto de carbono tende a ter vida útil mais longa.
Outra característica do concreto que usa armadura à base de fibras de carbono é que ele é 4 vezes mais resistente que o concreto convencional. “Isso permite projetar estruturas mais esbeltas, e que conseguem suportar cargas iguais a grandes estruturas de concreto armado”, diz o engenheiro civil e arquiteto Gunter Henn, da Henn Arquitetura, que projetou o edifício em construção na TU Dresden.
O prédio batizado de “The Cube” foi planejado para ter laboratórios e salas de evento. Henn projetou o edifício em parceria com o Instituto de Estruturas de Concreto da TU Dresden. “A meta é que a construção emita 50% menos CO₂ que uma construção convencional”, afirma o professor Manfred Curbach, que atua na universidade alemã.
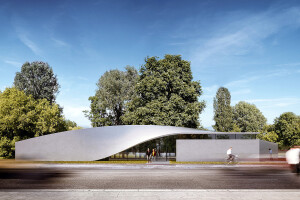
Crédito: Heen
A ideia é que o edifício seja uma vitrine para a pesquisa da TU Dresden chamada de C³ (Composto de Concreto de Carbono). Existe investimento do governo alemão no projeto, que passou a estimular estudos que criem materiais na construção mais sustentáveis. “Além de gerar estruturas com alto desempenho, o concreto de carbono permite desenhos arquitetônicos com mais curvas”, completa Henn.
Custo do concreto de carbono é estimado em 20 vezes mais caro que o concreto convencional
O “The Cube” terá 200 m² de área construída e também contará com paredes de vidro e estruturas de concreto armado nas partes menos desafiadoras da concepção arquitetônica, como o radier e as fundações. O maior volume de C³ será usado na construção de uma das paredes laterais do edifício, que avança para se transformar no teto da obra. Todos os elementos com concreto de carbono serão pré-fabricados. O prédio já se encontra em fase de execução e a previsão é que seja inaugurado no 1º semestre de 2022.
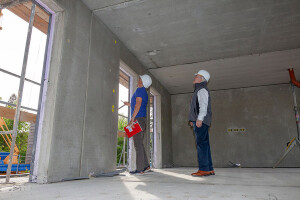
Crédito: Stefan Gröschel/TU Dresden
O custo do concreto de carbono é estimado em 20 vezes mais caro que o concreto armado convencional. “A redução de custos ocorrerá no futuro, à medida que as técnicas de adição de fibra de carbono ao concreto forem aprimoradas”, avalia Manfred Curbach. A construção do “The Cube” está estimada em 5 milhões de euros.
O concreto que usa armadura à base de fibras de carbono está em pesquisa na Alemanha desde 2008. Dentro do país, mais de 140 institutos de pesquisa, empresas de construção e instituições públicas estão envolvidos no estudo. O Ministério Federal da Educação e Pesquisa financia o trabalho interdisciplinar com um orçamento de 45 milhões de euros.
Também está em estudo na Alemanha o uso do concreto de carbono para restaurar pontes que estejam perto de completar 50 anos de vida útil. Estima-se que o material permita construir estruturas que suportem até 80 anos sem exigir manutenção.
Entrevistado
Escritório de arquitetura Henn e Instituto de Estruturas de Concreto da Universidade Tecnológica de Dresden
Contatos
info@henn.com
pressestelle@tu-dresden.de
Jornalista responsável:
Altair Santos MTB 2330