Pavimento urbano de concreto não aceita “jeitinho”
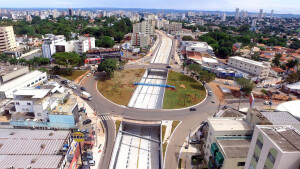
Crédito: Prefeitura de Goiânia
Seminário que encerrou a edição 2021 do Concrete Show Xperience tratou dos entraves que impedem o pavimento de concreto de avançar como solução urbana. Apesar de conseguir um volume maior de contratações por parte das prefeituras, o sistema ainda esbarra em aspectos culturais e no chamado “jeitinho brasileiro”, afirmam os debatedores que estiveram no evento virtual. Entre eles, Valter Frigieri, da ABCP; Eduardo Tarduce, consultor em pavimentação de concreto; Vagner Lopes, da Abesc, e João Batista Rodrigues da Silva, presidente do IBTS.
Valter Frigieri, diretor de planejamento e mercado da Associação Brasileira de Cimento Portland (ABCP), faz a seguinte análise: “Falta planejamento e urbanismo para as cidades pensarem em pavimento de concreto. As prefeituras não têm estrutura técnica de engenharia para viabilizar esse processo. Também tem o aspecto cultural calcado em cima do asfalto. Isso enraizou nos municípios. O asfalto é flexível também para criar obras superficiais, de aparência, mas sem durabilidade e que geram recapeamentos em série. Soluções baratas geram obras ruins.”
O dirigente da ABCP conclui que o pavimento de concreto não aceita “jeitinho”. “Ele requer planejamento, projeto e engenharia. As administrações públicas até começam a ter boa visão do concreto, mas a engrenagem das prefeituras ainda está montada para pavimentar com asfalto. Inclusive, o maquinário público. Isso gera estoques de passivos, pois uma avenida de asfalto vai requerer manutenção daqui a, no máximo, 5 anos”, alerta Frigieri, relacionando quais obras urbanas mais utilizam pavimento de concreto atualmente. “São os corredores de BRT, as avenidas, as ruas de bairros em cidades do interior – e com a participação das comunidades nas obras -, condomínios privados e ruas vicinais”, completa.
Estratégia de disseminação do sistema de paredes de concreto deve inspirar o pavimento urbano de concreto
Referindo-se à fala do diretor da ABCP, o consultor em pavimentação de concreto Eduardo Tarduce reforçou a necessidade de alterar essa visão do poder público. “Essa cultura a gente precisa mudar no Brasil. Até porque, o pavimento de concreto é o futuro”, afirma. Tarduce ressalta também que o aumento generalizado do preço do barril do petróleo tende a inviabilizar o custo do pavimento com asfalto. “O produto (petróleo) que está cada vez mais caro. Logo, futuramente será inviável fazer uso de asfalto e demais derivados do petróleo. Já o pavimento de concreto não tem esse problema, pois teremos a principal matéria-prima dele por muitos anos, em larga escala e a um preço barato, que é o cimento.
Já Wagner Lopes, presidente da Abesc (Associação Brasileira das Empresas de Serviços de Concretagem), reforça que em 2022 haverá um trabalho ainda mais fortalecido pelo pavimento urbano de concreto. O dirigente repete as vantagens do sistema. “Ele oferece uma série de benefícios às cidades. Além de minimizar o aquecimento das vias em até 2°C, reduz a emissão de CO₂, ajuda a economizar o consumo de energia elétrica das cidades e possui uma longa vida útil, comparado com o asfalto”, complementa.
Para finalizar, o diretor do Instituto Brasileiro de Telas Soldadas (IBTS), João Batista Rodrigues da Silva, defende que é necessário disseminar o pavimento urbano de concreto da mesma forma que ocorreu com as paredes de concreto. “Em 2007, quando nos reunimos para buscar uma melhor solução construtiva que atendesse as necessidades do mercado imobiliário nacional, nos deparamos com a ideia das paredes de concreto. Até então, o sistema era pouco utilizado no país e, hoje, é uma tecnologia de sucesso no Brasil. São mais de 200 construtoras fazendo uso deste modelo e mais de 70% das moradias dos programas habitacionais já utilizam o sistema. Agora, temos que adotar a mesma estratégia com os pavimentos urbanos de concreto”, conclui.
Assista à integra do seminário “Pavimento Urbano de Concreto”
Entrevistado
Reportagem com base no seminário “Pavimento Urbano de Concreto”, que ocorreu na 2ª edição da Concrete Show Xperience
Contato
concreteshow@go08.informamarkets.com
Jornalista responsável:
Altair Santos MTB 2330
Engenharia estrutural elege Ponte do Guaíba como a obra do ano
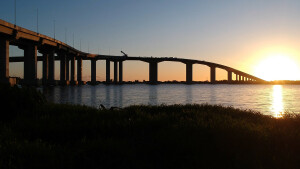
Crédito: DNIT
O 18º Prêmio Talento Engenharia Estrutural, promovido pela ABECE (Associação Brasileira de Engenharia e Consultoria Estrutural), elegeu a ponte sobre o Rio Guaíba a principal obra de infraestrutura do ano. O projeto estrutural é do professor-doutor da Escola Politécnica da USP, Fernando Rebouças Stucchi, reconhecido internacionalmente por seus conhecimentos sobre pontes e grandes estruturas.
Além de ser uma obra emblemática sobre o ponto de vista da engenharia, a Ponte do Guaíba é estratégica para a mobilidade urbana de Porto Alegre-RS e região metropolitana, além de fazer a ligação com a BR-116 no sentido porto de Rio Grande – o principal terminal de cargas do Rio Grande do Sul.
A execução da obra consumiu mais de 170 mil m3 de concreto pré-moldado e ajudou o Brasil a avançar casas em rankings internacionais de competitividade no quesito infraestrutura rodoviária. Em palestra no Instituto de Engenharia, concedida em 2018, Fernando Rebouças Stucchi revela detalhes do projeto estrutural da obra e de como foi a execução da ponte (acompanhe o vídeo no final da reportagem).
Faltam 4 alças de acesso à ponte para que projeto esteja 100% concluído
Inaugurada em 10 de dezembro de 2020, a ponte sobre o Guaíba começou a sair do papel em 2014, quando a execução foi homologada pelo DNIT (Departamento Nacional de Infraestrutura de Transportes). Nem todo o complexo rodoviário no entorno da ponte está concluído. Foram entregues 95% do projeto. Além do vão principal, mais 3 alças de acesso. Outras 4 alças de acesso só poderão ser construídas quando forem removidas as famílias que ocupam áreas nas vilas Areia e Tio Zeca, por onde deverão passar as superestruturas. O caso está na Justiça do Rio Grande do Sul.
Quase um ano depois da inauguração, a Ponte do Guaíba recebe diariamente um fluxo de quase 50 mil veículos por dia. Outros números superlativos envolvem a fase de construção da ponte. Na obra atuaram mais de 2 mil operários. Foram pré-moldados 15.250 elementos de concreto, entre estacas, blocos, vigas, pilares, aduelas e guarda-rodas. Os pesos das peças variaram entre 2,6 toneladas (guarda-rodas) a 100 toneladas (aduelas). Durante boa parte de sua execução, a Ponte do Guaíba foi considerada a principal obra rodoviária do Brasil.
Além do canteiro de obras na área de construção da ponte também foi instalado um canteiro industrial em Canoas-RS, na região metropolitana de Porto Alegre-RS. Nesse espaço é que foram pré-moldadas as estruturas de concreto. O transporte foi realizado por balsas pelo rio Guaíba, o que eliminou o risco de ter que interditar o trânsito naquela região da capital gaúcha.
Entrevistado
ABECE (Associação Brasileira de Engenharia e Consultoria Estrutural)
Instituto de Engenharia
DNIT (Departamento Nacional de Infraestrutura de Transportes)
Contato
abece@abece.com.br
atendimento@iengenharia.org.br
imprensa@dnit.gov.br
Jornalista responsável:
Altair Santos MTB 2330
Pesquisadores do MIT descobrem concreto de 2.050 anos
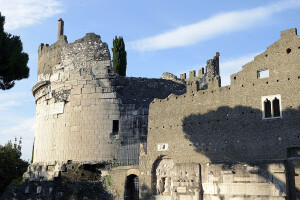
Crédito: MIT
Um pequeno castelo com 21 metros de altura e 29 metros de diâmetro, construído provavelmente entre os anos 30 a.C e 27 a.C, para abrigar túmulos de uma família aristocrática de Roma, se mantém intacto e pode ser uma das estruturas em concreto mais antigas do mundo. Pesquisadores do departamento de engenharia civil e ambiental do MIT (Massachusetts Institute of Technology) estimam que o concreto da construção possa ter 2.050 anos.
Apesar da longa idade, a estrutura mantém-se intacta, sem nenhum tipo de patologia. Para a equipe do MIT, a descoberta pode dar subsídios para pesquisas que levem a um tipo de concreto perpétuo, o que sob o ponto de vista de sustentabilidade seria um avanço significativo. “Estamos falando de construções intactas há mais de dois milênios”, diz Admir Masic, coordenador da pesquisa do MIT.
A primeira fase do estudo foi publicada no Journal of the American Ceramic Society. A análise conclui que o castelo-mortuário foi construído em alvenaria estrutural, com blocos maciços assentados para que as paredes da edificação tivessem 7 metros de espessura. Um dos segredos para a longa vida da edificação, avaliam os pesquisadores, é que foi utilizado como agregado do concreto o material que tem o nome científico de Pozzolane Rosse tephra, popularmente conhecida como pedra-pomes.
A pedra-pomes até hoje é usada como agregado leve na composição do concreto. Resumidamente, ela é um tipo de rocha vulcânica que se forma a partir dos gases expelidos na fase inicial de uma erupção. Em contato com o ar, esse gás resulta em uma espuma que, ao se solidificar, dá origem à pedra-pomes. No estudo publicado na Journal of the American Ceramic Society concluiu-se que o uso da Pozzolane Rosse tephra contribuiu para melhorar a reologia do concreto, em um ambiente de exposição à água.
Estudo revela que houve um “milagre estrutural” no concreto milenar
A pesquisa contou com a tecnologia conhecida como microscopia eletrônica de varredura. Ela analisou as microestruturas dos blocos de construção usados no castelo até a escala de mícrons. “Essas informações nos permitiram explorar diferentes áreas da argamassa e pudemos escolher os blocos de construção relacionados às nossas perguntas”, diz Linda Seymour, integrante da equipe do MIT. Os dados coletados permitiram que os pesquisadores descobrissem até de que vulcão vieram os agregados utilizados no concreto da obra milenar. Ele veio do Alban Hills, localizado na região de Lazio-Itália.
Para Admir Masic, a “sabedoria romana para construir obras perenes fornece uma estratégia sustentável que pode melhorar a longevidade de nossas construções modernas”. O professor do MIT e sua equipe citam ainda que houve algum “milagre estrutural” no concreto de 2.050 anos, que eles explicam da seguinte forma:
“Verificou-se que os elementos colantes da argamassa são ricos em cálcio-alumínio-silicato-hidrato (CASH) juntamente com cristais de estratlingita. Por outro lado, existe presença abundante de leucita, que é rica em potássio. Séculos de chuva e água subterrânea percolando as paredes da tumba dissolveram a leucita e liberaram o potássio na argamassa. No concreto moderno, uma abundância de potássio criaria géis expansivos que causariam microfissuras e eventual deterioração da estrutura.”
“Na tumba, porém, o potássio se dissolveu e reforçou os ligantes, criando componentes robustos de coesão no concreto. Precisamos entender o que mudou, e como mudou, ao longo dos séculos para aplicarmos os ensinamentos nos concretos modernos”, finaliza o estudo do departamento de engenharia civil e ambiental do MIT (Massachusetts Institute of Technology).
Entrevistado
Reportagem com base na pesquisa realizada pelo departamento de engenharia civil e ambiental do MIT (Massachusetts Institute of Technology)
Contato
one@mit.edu
Jornalista responsável:
Altair Santos MTB 2330
Casa Verde e Amarela: construtoras terão que fazer seguro pós-obra
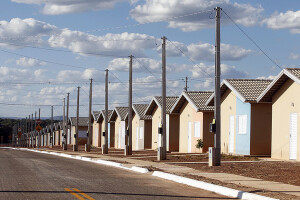
Crédito: MDR
A partir de 1º de janeiro de 2022, as construtoras credenciadas para atuar no programa Casa Verde e Amarela terão que fazer seguro pós-obra para cobrir eventuais danos estruturais nas unidades. O seguro deverá ter cobertura mínima de 5 anos. Trata-se de exigência da Secretaria Nacional de Habitação (SNH), vinculada ao ministério do Desenvolvimento Regional.
A SNH justifica a medida ao informar que atualmente 270 mil unidades do Minha Casa Minha Vida – programa antecessor do Casa Verde e Amarela – estão abandonadas pelos moradores por apresentarem problemas de construção, e que essas não possuem seguro para reparos.
“O seguro é para danos estruturais. Com isso, o governo reduz o risco de ser acionado na justiça para ter que cobrir prejuízos causados por erros estruturais na construção do imóvel, como estava acontecendo principalmente nos empreendimentos do grupo do programa Minha Casa Minha Vida que abrange a população de menor renda”, explica o secretário nacional de habitação do ministério de Desenvolvimento Regional, Alfredo Eduardo dos Santos.
O ministério de Desenvolvimento Regional já abriu negociações com 6 seguradoras, para que haja uma padronização no formato do seguro pós-obra e que o custo seja repassado o mínimo possível para o valor do imóvel. “O valor do seguro não será relevante. A ideia é que não represente aumento de custos, principalmente para as pequenas e médias construtoras credenciadas pelo programa”, assegura o secretário nacional da SNH. No novo modelo, a seguradora terá que acompanhar toda a execução da obra e, dentro do prazo de 5 anos após a entrega do imóvel, caso ocorra algum problema, terá que assumir os custos.
Número de construtoras credenciadas pelo Casa Verde e Amarela é menor que o do extinto Minha Casa Minha Vida
Segundo dados da Secretaria Nacional de Habitação, atualmente 2.039 construtoras estão credenciadas pelo Casa Verde e Amarela em todo o país. No auge do Minha Casa Minha Vida, em 2009, 2010, 2011 e 2012, eram 4.500. A expectativa da SNH é que a recente parceria com governos estaduais para estimular o programa habitacional possa compensar o valor do seguro pós-obra.
O secretário Alfredo Eduardo dos Santos informa que a opção pelo seguro pós-obra é apenas uma das medidas que buscam melhorar a qualidade das obras do Casa Verde e Amarela. “A SNH também tem tomado iniciativas para fomentar a industrialização e a inovação. Uma delas foi buscar convênio com a ABNT (Associação Brasileira de Normas Técnicas) para a autorização de novos processos construtivos. A outra tem sido articular com o Sistema S o fomento de inovações na construção civil”, revela.
Recentemente, o PBQP-H (Programa Brasileiro da Qualidade e Produtividade do Habitat) lançou concurso para prospectar sistemas inovadores para a construção de habitações populares. Também este ano, o PBQP-H passou a incorporar a construção sustentável em seus protocolos.
Entrevistado
Secretaria Nacional de Habitação
Contato
snh@mdr.gov.br
Jornalista responsável:
Altair Santos MTB 2330
Mundo aposta em obras para recuperar perdas de 2020 e 2021
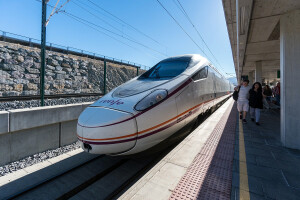
Crédito: PxHere
O programa de investimento em obras na ordem de 1 trilhão de dólares que os Estados Unidos começam a executar a partir de 2022 inspira outros países a irem pelo mesmo caminho: estimular a construção civil para gerar empregos e movimentar suas respectivas economias, após quase 2 anos de pandemia.
O governo Joe Biden sancionou o plano norte-americano no dia 15 de novembro. Do dinheiro liberado para uma série de obras, 110 bilhões de dólares serão investidos na recuperação e construção de estradas, pontes e viadutos.
Outros 66 bilhões de dólares vão para a infraestrutura ferroviária. Mais 39 bilhões irão para o transporte público, como obras para metrôs e BRTs (Bus Rapid Transit). Haverá também investimento de 55 bilhões de dólares para a recuperação do saneamento básico nas principais cidades dos EUA. A previsão é que todas as obras sejam concluídas no prazo de 5 anos.
Plano semelhante também foi anunciado na Grã-Bretanha, que colocará em ação 12 megaprojetos rodoviários e ferroviários, na ordem de quase 18 bilhões de libras (24 bilhões de dólares). A cena se repete na União Europeia, que já anunciou um pacote de 30 bilhões de euros (33 bilhões de dólares) para a região, que serão investidos entre 2022 e 2027.
A prioridade é o programa “Interligar a Europa”, cujo objetivo é unir por trens de alta velocidade os 28 países-membros do bloco. Do total de recursos, 23 bilhões de euros (25 bilhões de dólares) irão para esse modelo de infraestrutura. Planos semelhantes se estendem pela Ásia e pela América Latina.
Venda global de equipamentos para obras bate recorde
Por isso, já existem sinais evidentes de que a construção civil será a aposta da economia mundial para que sejam retomados índices de crescimento do período pré-pandemia. Um deles é o de venda global de equipamentos para a construção, que já atingiu um recorde em 2021. Segundo levantamento da consultoria britânica Off-Highway Research, foram vendidos este ano 1,13 milhão de motoniveladoras, caminhões, pás-carregadeiras, betoneiras, retroescavadeiras, guindastes e outras máquinas similares em todo o planeta.
O recorde anterior era de 2018, com a venda de 1,11 milhão de equipamentos. As vendas foram impulsionadas pelas compras realizadas na China, na Europa e nos Estados Unidos. De acordo com Chris Sleight, diretor da Off-Highway Research, a tendência é que o volume de negócios se mantenha aquecido também no ano que vem. “Espera-se que continue em 2022, pois diversos fabricantes vêm relatando pedidos para toda a produção em andamento”, diz.
Ou seja, as empreiteiras e construtoras já estão prontas para o volume de obras que deve começar em 2022. No Brasil, existe a expectativa de que o mercado de máquinas para a construção civil cresça entre 25% e 30% na comparação com 2020. O foco do investimento está nas obras desencadeadas pelas concessões de rodovias, ferrovias, portos e aeroportos.
Entrevistado
Consultoria britânica Off-Highway Research (via assessoria de imprensa)
Associated General Contractors of America (via assessoria de comunicação)
União Europeia (via assessoria de imprensa)
Departamento de Estratégia da Infraestrutura Nacional do Reino Unido (via assessoria de imprensa)
Contatos
mail@offhighwayresearch.com
info@agc.org
https://european-union.europa.eu/contact-eu/press-contacts_pt
MediaRelations@ipo.gov.uk
Jornalista responsável:
Altair Santos MTB 2330
Turquia constrói a maior ponte pênsil do mundo
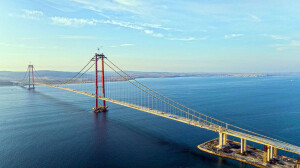
Crédito: Ministério dos Transportes e Infraestrutura da Turquia
A 1915Çanakkale, com previsão para ser inaugurada em 2023, será a maior ponte pênsil do mundo, tanto em comprimento quanto em altura. Em construção desde 2017, seu vão central terá 2.023 metros e o ponto mais alto de suas duas torres estará a 334 metros acima das águas do estreito de Çanakkale, na Turquia.
Os números que envolvem a ponte estão cercados de simbolismos. A extensão de 2.023 metros faz referência ao ano de 2023, quando a Turquia comemora 100 anos de república. O ano de 1915 está relacionado com o fato de que, desde aquele ano, os turcos planejavam construir uma ponte no local.
Quando liberada para o tráfego de veículos, a 1915Çanakkale irá encurtar a distância entre Europa e Ásia. A ponte terá comprimento total de 4.608 metros, com seis faixas (3 em cada sentido). Um complexo rodoviário também está em construção para atender o fluxo de veículos sobre a obra de arte especial.
Esse complexo rodoviário abrange 324 quilômetros e contará ainda com 6 viadutos, 55 pontes de pequeno e médio portes, 40 passagens inferiores, 12 cruzamentos, 4 áreas de serviço da autoestrada, 2 centros de operação e manutenção e 7 praças de pedágio. O custo da obra está orçado em 2,3 bilhões de euros.
A ponte é executada por um consórcio de empreiteiras chinesas e turcas. O último deck de concreto que faltava para a conclusão do tabuleiro foi instalado em setembro de 2021, de um total de 96 em cada um dos sentidos da obra de arte especial. Cada peça pré-fabricada tem 45 metros de largura, 48 metros de comprimento e 700 toneladas de peso.
Consumo estimado de concreto é recorde na Turquia e chega a 385 mil m³
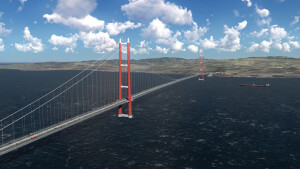
Crédito: 1915Çanakkale
O recorde de maior ponte suspensa do mundo irá para a 1915Çanakkale porque seu vão central de 2.023 metros vai superar o da Akashi Kaikyo, localizada no Japão, e que mede 1.992 metros. Ela também será a obra de arte especial construída na Turquia que mais terá consumido concreto. O total estimado é de 385 mil m³.
O projeto estrutural da ponte prevê vida útil de 120 anos. O estudo foi desenvolvido em parceria com 3 universidades turcas, que cederam seus laboratórios para os ensaios dos materiais empregados na construção, incluindo o concreto de alta resistência de 100 MPa. As fundações da 1915Çanakkale estão a 45 metros de profundidade.
O consórcio chinês formado pelas empreiteiras Daelim e SK E&C, juntamente com as empresas turcas Limak Holding e Yapi Merkezi, é responsável pela construção da ponte e irá operar o pedágio por 16 anos. A joint venture Parsons e Tekfen Engineering foi contratada para fornecer suporte de engenharia e construção, juntamente com serviços de supervisão e inspeção.
Já os consultores de engenharia da Pyunghwa forneceram o estudo de viabilidade e o projeto básico, enquanto a Pell Frischmann envolveu-se no desenvolvimento do projeto da 1915Çanakkale. No pico da obra, em 2019, 5.200 operários estavam trabalhando na construção da ponte.
Antes da megaestrutura, a travessia do estreito de Çanakkale era feito por balsa, com duração média de 45 minutos. Quando a ponte estiver inaugurada, o trecho será percorrido em 6 minutos.
Entrevistado
Consórcio 1915Çanakkale e ministério dos Transportes e Infraestrutura da Turquia (via assessorias de imprensa)
Contatos
info@1915canakkale.com
www.uab.gov.tr
Jornalista responsável:
Altair Santos MTB 2330
A um ano da Copa do Mundo, veja as obras no Catar
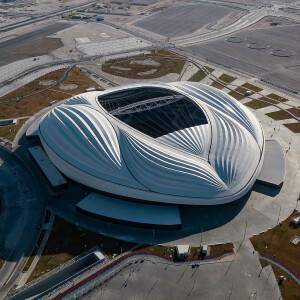
Crédito: Qatar's Supreme Committee for Delivery & Legacy
Se dependesse do ritmo das obras, a Copa do Mundo no Catar, que será disputada de 21 de novembro a 18 de dezembro de 2022, nem precisaria esperar mais um ano para começar. Quase toda a infraestrutura planejada para o evento já está concluída. Dos 8 estádios que receberão jogos, 6 já foram inaugurados. Os demais devem ficar prontos até o final do 1º trimestre de 2022, assim como as novas linhas de metrô e outros projetos que facilitam a mobilidade urbana no país árabe.
O mais recente estádio concluído é Al Thumama, que ficou pronto no final de outubro. A arena localizada em Doha, capital do Catar, tem 40 mil lugares e formato que imita um chapéu tradicional usado pelos árabes, chamado de gahfiya. Os outros estádios já prontos para a Copa do Mundo são o Khalifa International, o Al Janoub, o Education City, o Ahmad Bin Ali e o Al Bayt. Todos possuem sistema para resfriar o ar nas arquibancadas e no campo. A tecnologia utiliza grandes ventiladores alimentados por energia solar.
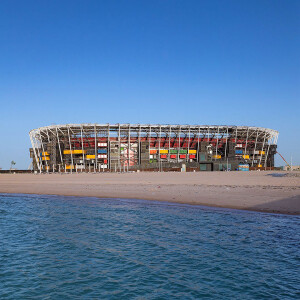
Crédito: Qatar's Supreme Committee for Delivery & Legacy
Após o evento da Fifa, os estádios da Copa do Catar serão desmontados parcialmente ou integralmente. O Al Thumama, por exemplo, ficará com 20 mil lugares e a área que será retirada dará lugar a um hotel. As partes desativadas dos estádios não serão demolidas, mas doadas para países pobres da África e da Ásia, através de programas da Fifa para a disseminação do futebol.
Construção industrializada de concreto é predominante nos projetos dos estádios
Todos os 8 estádios utilizaram a pré-fabricação e a construção modular para serem erguidos. Quatro deles - os que comportam mais público - foram 100% construídos com elementos pré-fabricados de concreto (Khalifa International, Education City, Al Thumama e Lusail). Três (Al Bayt, Al Janoub e Ahmad Bin Ali) usam sistemas mistos de concreto e aço em seus projetos e um deles, o Ras Abu Aboud, utiliza estruturas de aço e contêineres.
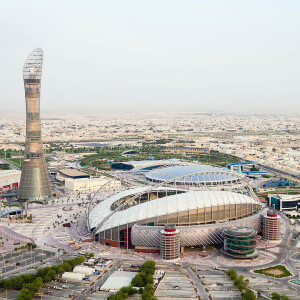
Crédito: Qatar's Supreme Committee for Delivery & Legacy
Os estádios que estão na reta final de execução são o Lusail, com capacidade para 80 mil lugares, e que será o palco da final da Copa do Mundo, e o Ras Abu Aboud. O Catar priorizou a mobilidade urbana. Por isso, a maior distância a ser percorrida entre os estádios equivale a uma hora de deslocamento por via terrestre. Cinco localizações foram contempladas como cidades-sede: Doha, que tem 3 estádios (Khalifa International, Al Thumama e Ras Abu Aboud); Al Rayyan, com 2 estádios (Education City e Ahmad Bin Ali), e Lusail, Al Khor e Al Wakrah.
Com população de quase 2,3 milhões de habitantes, o Catar atualmente é considerado o país mais rico do Oriente Médio. O investimento para promover a Copa do Mundo já está em 138 bilhões de dólares. Além de construir os estádios e a infraestrutura de mobilidade urbana, o país colocou em pé a cidade de Lusail - a primeira cidade-inteligente do mundo árabe - e viabilizou uma ferrovia com trens de alta velocidade que percorre 1.940 quilômetros e liga o Catar a outros 5 países: Omã, Emirados Árabes Unidos, Arábia Saudita, Kuwait e Bahrein.
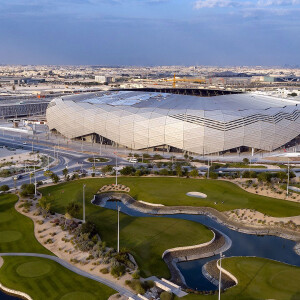
Crédito: Qatar's Supreme Committee for Delivery & Legacy
Entrevistado
Supremo Comitê da Copa de 2022 (Supreme Committee for Delivery & Legacy) (via assessoria de imprensa)
Contato
media@sc.qa
Jornalista responsável:
Altair Santos MTB 2330
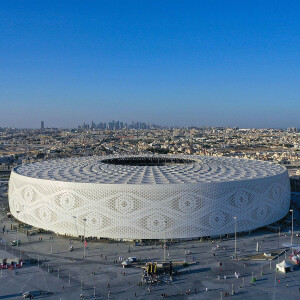
Crédito: Qatar's Supreme Committee for Delivery & Legacy
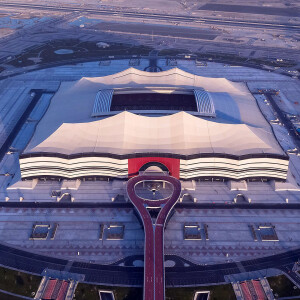
Crédito: Qatar's Supreme Committee for Delivery & Legacy
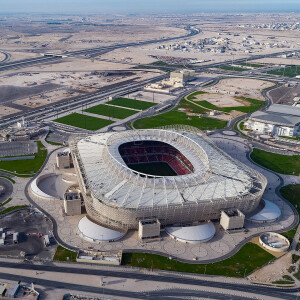
Crédito: Qatar's Supreme Committee for Delivery & Legacy
Aos 20 anos, Abcic move a construção industrializada no Brasil
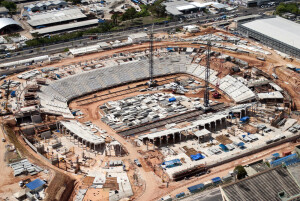
Crédito: EBC
Em 2001, foi criada a Abcic (Associação Brasileira da Construção Industrializada de Concreto). Com 20 anos completados em outubro de 2021, a organização é responsável por mudar paradigmas no setor da construção civil. Ao trazer para o país modelos de controles de qualidade praticados pela fib (International Federation for Structural Concrete) a associação chancelou a tecnologia de pré-fabricados e pré-moldados de concreto, e concedeu credibilidade aos sistemas construtivos com essas características.
Na entrevista a seguir, a engenheira civil Íria Doniak, presidente-executiva da Abcic, relata os avanços obtidos pela associação e os desafios que o setor terá que superar para se aproximar de números que já são realidade em países do hemisfério norte. Desde a criação da Abcic, a participação da pré-fabricação de concreto no mercado da construção civil nacional praticamente dobrou. Confira:
A Abcic acaba de completar 20 anos. Quais paradigmas foram rompidos com o surgimento da associação?
A criação da Abcic mostrou a união do setor e a iniciativa das indústrias de pré-fabricação de concreto para colocar em discussão as pautas mais importantes para o desenvolvimento do sistema construtivo que ela representa no país, como a padronização, a qualidade e a ética. Desse modo, a Abcic marcou uma nova trajetória para a construção industrializada de concreto no Brasil, porque a entidade passou a atuar em todos os contextos que viabilizam o desenvolvimento global da cadeia produtiva, desde os aspectos técnicos e de tecnologia, passando por ações internacionais, institucionais, governamentais e políticas, até questões de grande relevância para a construção civil, como competitividade e produtividade.
Logo que foi fundada, quais foram as primeiras ações da Abcic?
As primeiras ações estabelecidas estavam ligadas ao aspecto da qualidade e padronização. A primeira ação desenvolvida foi o Selo de Excelência Abcic, cujo início da implementação nas empresas ocorreu em 2003. O programa atesta as empresas quanto à qualidade, segurança e meio ambiente, incluindo, além das plantas de produção, os canteiros de obras. Em paralelo, a Abcic propôs à ABNT (Associação Brasileira de Normas Técnicas) a revisão da principal norma do setor no país: a ABNT NBR 9062 – Projeto e Execução de Estruturas de Concreto Pré-Moldado, cuja publicação ocorreu em 2006. Tal ação foi fundamental, pois a revisão anterior datava de 1985 e, para termos parâmetros a serem inseridos no selo, eles deveriam estar alinhados com a normalização internacional e com os novos métodos de produção, bem como a interface com a ABNT NBR 6118, relacionada aos projetos de estruturas de concreto.
A Abcic também aproximou o setor brasileiro da construção industrializada do concreto de organismos internacionais, correto?
Começamos a atuar na fib (International Federation for Structural Concrete), junto à comissão de pré-fabricação que reúne experts de todo o mundo, o que acelerou a pesquisa aplicada no Brasil e auxiliou sobremaneira o desenvolvimento da nossa normalização. Através do NETPRÉ (Núcleo de Estudos e Tecnologia da Pré-fabricação) – outra ação importante do setor -, em convênio com a UFSCar e a liderança do professor Marcelo Araújo Ferreira, estudos e pesquisas de cisalhamento e compressão de lajes alveolares e ligações em escala real foram desenvolvidos e apresentados fora do Brasil, o que possibilitou o debate e o aperfeiçoamento das propostas de normalização.
Como surgiu a ideia de criar o Prêmio Obra do Ano em Pré-Fabricados de Concreto, que completa 10 anos?
Nosso trabalho para desmistificar a crença de que a construção industrializada do concreto tolhia a liberdade criativa do arquiteto resultou na criação do prêmio, através de um trabalho em conjunto com o IAB (Instituto de Arquitetos do Brasil). Inicialmente, surgiu como um prêmio para estimular estudantes de arquitetura. Posteriormente, passou a abranger profissionais. Um de seus fundamentos é promover a sinergia entre a execução das obras, a arquitetura e os projetos de estruturas.
Nesses 20 anos, é possível estimar o quanto a construção industrializada de concreto evoluiu no Brasil?
Duas lições importantes foram aprendidas nestes 20 anos. A primeira, pensar globalmente e agir localmente. A segunda, construir “pontes”, pois ninguém faz nada sozinho. A integração dos elos da cadeia produtiva permitiu galgar cada vez mais o número de pavimentos em edifícios comerciais e residenciais, com soluções integralmente pré-fabricadas ou combinadas. Hoje, estamos presentes em diversos segmentos de forma expressiva. Não somente nos tradicionais, como indústrias, varejo, centros de distribuição e logística, hoteleiro, mas também nas áreas de educação, hospitalar, edifícios-garagem, infraestrutura – aeroportuária, rodoviária e portuária -, mobilidade urbana (BRTs e estações de metrô), estádios, edifícios comerciais e residenciais. Enfim, uma infinidade de aplicações. Os eventos esportivos que o Brasil sediou em 2007 (Jogos Pan-americanos), 2014 (Copa do Mundo) e 2016 (Olimpíadas) deixaram um legado importante para a construção industrializada do concreto. Criou-se um movimento “pró-industrialização” importante no país. Creio que, se considerarmos o percentual sobre o total de estruturas, fachadas e fundações produzidas nestes 20 anos, quase dobramos a participação da pré-fabricação no mercado, indo de 4 a 5% para 8 a 10%. É apenas uma estimativa, pois não existe ainda um dado confiável do share dos sistemas construtivos. Mas isso ainda é um índice muito baixo, se compararmos especialmente com a Europa, que varia de 30% a 90%, sendo que os índices mais altos são alcançados nos países nórdicos, além de Holanda e Bélgica.
E quais são as barreiras que ainda precisam ser superadas?
Ao longo deste período trabalhamos muito para vencer desafios ligados às barreiras que ainda impedem o avanço da industrialização na construção civil, como a tributação e os modelos de financiamento e licitações. São áreas em que temos militado, mas ainda temos muito a fazer. Este é um outro trabalho forte da Abcic, e muito extenso.
Antes do surgimento da Abcic, como era a construção industrializada de concreto no Brasil?
As obras pré-moldadas começaram a aparecer com maior frequência ao final da década de 1950, destacando-se a obra industrial do Curtume Franco Brasileiro, em Barueri-SP, que utilizou concreto pré-moldado em canteiro na execução dos pavilhões da fábrica. Outro importante marco foi em 1962, em que foram utilizadas placas pré-moldadas e vigas pré-moldadas protendidas nos prédios de escritórios e almoxarifados do setor norte do campus da Universidade de Brasília (UnB), projetado pelo arquiteto Oscar Niemeyer. Nos anos 1970, com o início do chamado “Milagre Brasileiro”, o Brasil era considerado como o país do futuro, e o investimento em tecnologia promoveu a ampliação das possibilidades de aplicações do concreto pré-moldado. No início dos anos 1980, a pré-fabricação começou a ter maior visibilidade na execução de obras industriais e especialmente em obras de empresas multinacionais. Nos anos 1990, as grandes redes de hipermercados aderiram à construção industrializada. O sistema avançou para a construção de shopping centers e centros de distribuição e logística. O fato da Abcic ter especialmente organizado a questão da padronização e normalização, consideradas a base de desenvolvimento sustentável de um setor, possibilitou um grande apoio para os projetistas e para a indústria da construção, formando uma base importante para o desenvolvimento tecnológico e o avanço do nosso segmento.
Quais as metas e desafios da Abcic para os próximos anos?
As metas da Abcic estão ligadas sempre ao desenvolvimento sustentável do setor. Por isso, superar os desafios contribui para alcançarmos esse objetivo. Nesse sentido, o principal deles continua a ser a disparidade tributária existente entre os sistemas produzidos em fábrica, chamados de industrializados, e a construção nos métodos convencionais ou racionalizados, executados no próprio canteiro de obras. Também vamos continuar nosso trabalho de disseminação dos benefícios da industrialização durante todo o ciclo de vida do empreendimento, ou seja, mostrando que é preciso mudar a mentalidade de custo por m2 pela visão integral do ciclo de vida. Essa disseminação também passa pelo estímulo a uma melhor capacitação da mão de obra intelectual e revisão dos currículos das escolas de engenharia e arquitetura. Entendemos que é necessário promover uma revisão geral nos métodos de formação dos profissionais. Outro ponto é o estímulo ao emprego cada vez maior de novas tecnologias, seja nos materiais, nos processos de produção, em equipamentos, na digitalização e nas ferramentas da indústria 4.0, que possuem total sinergia com a industrialização. Além disso, defendemos o uso cada vez maior do BIM, em suas variadas dimensões. Também existe a expectativa de que outros aspectos tecnológicos nos trarão mais competitividade, como a adoção do UHPC (Ultra High Performance Concrete) e da impressão 3D.
Por fim, a Abcic está confiante no Brasil. Quais projeções a associação faz para o setor em 2022?
A expectativa é que nosso setor acompanhe a esperada retomada na área da construção. Contudo, isso ainda vai depender de alguns pontos, como o retorno dos investimentos nacionais e internacionais, a capacidade do governo lidar com a economia em geral, e, é claro, avançar com o programa de vacinação e sanar a pandemia. Antes da crise sanitária e da crise econômica anterior, a industrialização vinha crescendo de forma bastante acelerada, por todos os benefícios que oferece, incluindo mais qualidade, produtividade, segurança, sustentabilidade, otimização de custos, menor tempo de construção, entre outros. Esses são os motivos pelos quais há um movimento pela industrialização na construção civil.
Entrevistada
Engenheira civil Íria Doniak, presidente-executiva da Abcic (Associação Brasileira da Construção Industrializada de Concreto)
Contato
abcic@abcic.org.br
Jornalista responsável:
Altair Santos MTB 2330
Norma admite agregados reciclados em concreto estrutural
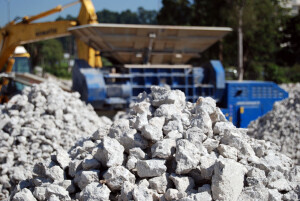
Crédito: Abrecon
O CB-018 (Comitê Brasileiro de Cimento, Concreto e Agregados), vinculado à ABNT, publicou em junho a nova versão da ABNT NBR 15116:2021 (Agregados reciclados para uso em argamassas e concretos de Cimento Portland – Requisitos e métodos de ensaios). A anterior era de 2004. A norma especifica os critérios para produção, recepção e uso dos agregados reciclados (miúdos e graúdos) obtidos a partir do beneficiamento de resíduos da construção civil (RCC). A novidade da ABNT NBR 15116:2021 é que ela agora admite esse tipo de agregado em concretos estruturais. A versão antiga recomendava o uso apenas em concretos sem função estrutural.
A nova norma técnica define que não é qualquer agregado reciclado que serve para produzir concreto estrutural. A ABNT NBR 15116:2021 separa os resíduos da construção civil em “classes A, B, C e D”. Apenas o de classe A é recomendado. Trata-se do agregado graúdo de resíduo de concreto, cujas especificações são as seguintes, diz a norma: “Deve ser composto na sua fração graúda de, no mínimo, 90% em massa de fragmentos à base de Cimento Portland e rochas”. Ou seja, além de ser da classe A, o resíduo deve pertencer à subclasse ARCO, que significa Agregado Reciclado de Concreto (ARCO).
As outras duas subclasses da classe A são o Agregado Reciclado Cimentício (ARCI) e o Agregado Reciclado Misto (ARM), mas essas não são aceitas pela norma para a produção de concreto estrutural. Além disso, ela define o percentual que pode ser incluído na mistura. Diz o trecho da ABNT NBR 15116:2021: “Admite a possibilidade do uso de agregados reciclados para dosagens de concretos com fins estruturais, desde que sejam respeitadas as devidas recomendações: uso restrito de ARCO, teor de substituição de 20% dos agregados convencionais pelo reciclado e uso em concretos das classes de agressividade I e II, de acordo com a ABNT NBR 6118:2014.”
Agregados reciclados são admitidos para a produção de concretos estruturais com resistência máxima de 20 MPa
As classes de agressividade I e II referem-se a ambientes em que o risco de deterioração das estruturas é insignificante ou pequeno. Além disso, a ABNT NBR 15116:2021 aconselha o uso de agregados reciclados para a produção de concretos estruturais com resistência máxima de 20 MPa – geralmente usados para a construção de obras leves e unidades unifamiliares de até 2 pavimentos (casas e sobrados). Em laboratório, concretos com agregados reciclados, que são entre 60% e 70% menos resistentes do que os que utilizam brita, já atingiram 45 MPa. Isso foi obtido em ensaios realizados na Alemanha, na Inglaterra, na Suíça e na Índia, que há anos desenvolvem pesquisas para obter concretos estruturais usando agregados reciclados.
Além de seguir os requisitos da ABNT NBR 15116:2021, o CB-018 recomenda que o concreto estrutural que utilizar agregados reciclados deve atender também a ABNT NBR 6118 (Estruturas de concreto armado), a ABNT NBR 7211 (Agregados para concreto – Especificações) e a ABNT NBR 16917 (Agregado graúdo – Determinação da densidade e da absorção de água) também recentemente revisada pelo Comitê Brasileiro de Cimento, Concreto e Agregados. Segundo a Abrecon (Associação Brasileira para Reciclagem de Resíduos da Construção Civil e Demolição) a revisão da ABNT NBR 15116:2021 deve levar também à revisão das outras 4 normas técnicas correlatas, que são:
– ABNT NBR 15115:2004 – Agregados reciclados de resíduos sólidos da construção civil – Execução de camadas de pavimentação – Procedimentos
– ABNT NBR 15114:2004 – Resíduos sólidos da Construção civil – Áreas de reciclagem – Diretrizes para projeto, implantação e operação
– ABNT NBR 15113:2004 – Resíduos sólidos da construção civil e resíduos inertes – Aterros – Diretrizes para projeto, implantação e operação
– ABNT NBR 15112:2004 – Resíduos da construção civil e resíduos volumosos – Áreas de transbordo e triagem – Diretrizes para projeto, implantação e operação
Entrevistados
CB-018 (Comitê Brasileiro de Cimento, Concreto e Agregados) e Abrecon (Associação Brasileira para Reciclagem de Resíduos da Construção Civil e Demolição) (via assessorias de imprensa)
Contatos
impresa@abnt.org.br
rcd@abrecon.org.br
Jornalista responsável:
Altair Santos MTB 2330
Meta da indústria do cimento é emissão zero de CO₂ até 2050
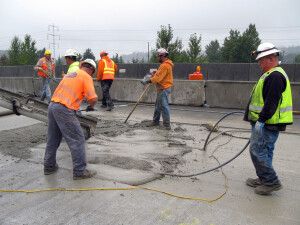
Crédito: WSDOT
A Global Cement and Concrete Association (GCCA) – Associação Global de Cimento e Concreto – anuncia que as indústrias responsáveis por 80% da produção de cimento nos países ocidentais chegaram a um acordo sobre as 7 principais metas a serem alcançadas em 2050, a fim de que o setor zere a emissão de carbono no processo de fabricação do insumo.
Para obter emissão zero é necessário compensar o CO₂ emitido. Assim, os objetivos para se chegar ao 100% de compensação são os seguintes:
1. Eliminar 22% das emissões
2. Aumentar em 11% a eficácia na produção de cimento
3. Melhorar em 9% o desempenho do cimento e os demais ligantes na produção de concreto
4. Descarbonização do clínquer em 11%
5. Capturar e armazenar no concreto 36% do CO₂
6. Elevar em 5% a transição para energias renováveis
7. Reduzir em 6% a carbonatação natural do concreto armado
O acordo entre as cimenteiras ocidentais foi divulgado dia 12 de outubro de 2021, em Londres-Inglaterra, semanas antes da 26ª Conferência das Nações Unidas sobre Mudanças Climáticas, a COP-26, que acontece até dia 12 de novembro em Glasgow-Escócia. O documento não foi assinado pelas cimenteiras chinesas, mas a China National Building Material – organismo que regulamenta a produção de cimento no país – prometeu tomar medidas para mitigar a emissão de CO₂ de sua indústria.
A Global Cement and Concrete Association definiu as metas como “um passo importante para eliminar a pegada de CO₂ do concreto”. O documento, que leva o nome de “Concreto Net Zero em 2050”, também tem entre suas cláusulas o compromisso do setor de reduzir em mais de 25% as emissões de CO₂ até 2030. A GCCA reúne cimenteiras da Europa, das Américas do Norte, Central e Sul, da África e da Ásia.
O CEO da GCCA, Thomas Guillot, fala da importância do acordo. “A cooperação global na descarbonização de concreto é uma necessidade, já que os países que estão desenvolvendo sua infraestrutura e habitações serão os maiores usuários de concreto nas próximas décadas”, diz. Guillot também pediu a parceria dos governos para ajudar no cumprimento das metas. “Precisamos do apoio deles para mudar a regulamentação que limita o uso de materiais reciclados e impede a transição para uma economia circular e de baixo carbono”, completa.
À COP-26, Brasil informa que tem a indústria cimenteira menos agressiva do mundo
No Brasil, o SNIC (Sindicato Nacional da Indústria do Cimento) e a ABCP (Associação Brasileira de Cimento Portland) enviaram documento à COP-26 mostrando que no país o setor é um dos menos agressivos do mundo. “Dentre as iniciativas promovidas pelas empresas estão o uso de matérias-primas alternativas (fíler calcário, escórias siderúrgicas e cinzas de termelétricas, por exemplo) e de combustíveis alternativos, tais como biomassas, resíduos industriais, comerciais e domésticos, pneus, entre outros. Essas ações elevaram o Brasil à condição de referência global como o país que menos emite CO₂ por tonelada de cimento produzida no mundo”, afirma o relatório enviado a Glasgow.
Enquanto a indústria de cimento global responde por 7% da emissão de CO₂, no Brasil o setor emite apenas 2,3% do volume de gás carbônico lançado na atmosfera, segundo dados do Inventário Nacional de Emissões e Remoções Antrópicas de Gases de Efeito Estufa não Controlados pelo Protocolo de Montreal. Segundo o presidente do SNIC e da ABCP, Paulo Camillo Penna, a indústria cimenteira nacional tem a meta de reduzir em 33% suas emissões até 2050. “Isso evitará a emissão de 420 milhões de toneladas de CO₂ e implicará na redução da intensidade carbônica do cimento brasileiro de 564 quilos por tonelada para 375 quilos por tonelada, tornando-se a menor do planeta”, afirma.
Clique e saiba mais sobre o relatório da GCCA
Entrevistado
Reportagem com base no Roadmap da Global Cement and Concrete Association (GCCA) para chegar ao NET Zero do Concreto em 2050
Contato
info@gccassociation.org
Jornalista responsável:
Altair Santos MTB 2330