Brasil atrai escritórios internacionais de engenharia
Projeção obtida pelo país lá fora, por causa de eventos como Copa do Mundo e Olimpíadas, desperta interesse global; ABECE alerta para qualidade dos projetos
Por: Altair Santos
A projeção internacional obtida pelo Brasil com eventos como Copa do Mundo e Olimpíadas atraiu alguns dos principais escritórios de engenharia e consultoria do mundo. Estima-se que atualmente pelo menos 40 empresas tenham aberto filiais no país ou estejam atuando em parceria com outras companhias nacionais especializadas em engenharia estrutural, consultoria e projetos. São principalmente norte-americanos, ingleses, alemães e espanhóis, que estão envolvidos não apenas na construção de equipamentos esportivos, mas em obras de infraestrutura, aeroportuárias e de alto padrão no setor de habitação e escritórios.
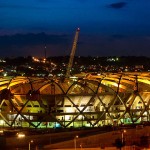
O auge da chegada de escritórios multinacionais de engenharia aconteceu entre 2008 e 2012. Hoje, as empresas consolidadas no país têm se dedicado a prospectar novos mercados na América Latina. É o caso da inglesa Arup, conhecida mundialmente por projetar obras como a Sydney Opera House (Austrália), o trem bala Londres-Paris High Speed 1 (Inglaterra), o centro aquático Cubo D´água (China) e as arenas esportivas Ninho do Pássaro (China) e a Allianz Arena (Alemanha). "Desejamos expandir nossas atividades por aqui e por todo o Mercosul. Contamos com um escritório em São Paulo desde 2012 e há cerca de três meses abrimos outro no Rio de Janeiro", diz o diretor da empresa no Brasil, Ricardo Pittella.
O CEO da Arup no país explica o porquê de as empresas estarem conseguindo ampliar suas carteiras no Brasil. "Existem poucas empresas de engenharia de projetos que atendam a praticamente todos os segmentos e ofereçam soluções multidisciplinares. Além disso, a cooperação e troca de conhecimentos globais entre os escritórios é muito intensa", completa. Foi isso que atraiu também as alemãs GMP (Gerkan, Marg und Partner) e a norte-americana Populous, que desembarcaram no Brasil assinando os projetos de reforma do Maracanã e da nova Arena das Dunas, em Natal - ambos prontos para receber jogos da Copa do Mundo.
Outro grupo consolidado no Brasil é o espanhol Sener. Instalada desde 2009, a empresa tem atualmente 300 profissionais entre engenheiros, projetistas e arquitetos trabalhando no país. A divisão brasileira desenvolve projetos nos setores de energia e processos, engenharia civil e arquitetura, aeroespacial e naval. Petrobras, BR Distribuidora, Construtora Norberto Odebrecht, Embraer e o estaleiro STX, em Niterói-RJ, estão entre os clientes da companhia espanhola.
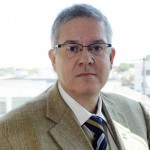
A concorrência internacional estimulou escritórios brasileiros a se associarem com parceiros de fora, mas, no entender da ABECE (Associação Brasileira de Engenharia e Consultoria Estrutura) essa abertura deve ser vista com senso crítico. "Nosso mercado não é tão grande e tão abrangente assim, e não há falta de profissionais no país", avalia João Alberto de Abreu Vendramini, vice-presidente de marketing da ABECE, completando que esse movimento pode prejudicar a formação de novos engenheiros estruturais no Brasil, já que a maioria destes escritórios traz profissionais de fora. "Esse é um setor estratégico para o país, que precisaria de reserva de mercado. Será que precisamos desta mão de obra estrangeira?", questiona.
Entrevistados
Engenheiros civis Alberto de Abreu Vendramini, vice-presidente de marketing da ABECE, e
Ricardo Pittella, diretor da Arup no Brasil
Contatos
americas@arup.com
abece@abece.com.br
Créditos Fotos: Divulgação/Secopa-AM/ABECE
Jornalista responsável: Altair Santos MTB 2330
Automação eleva produtividade no canteiro de obras
Uso de máquinas com alta tecnologia reduz sensivelmente o retrabalho, mas exige mão de obra cada vez mais qualificada
Por: Altair Santos
A gestão eficiente de equipamentos projetados para a construção civil aumenta a produtividade no canteiro de obras, principalmente quando se investe em automação de máquinas. É o que comprovam experiências realizadas por algumas das grandes construtoras do Brasil, que ao investir em tecnologia buscam também diminuir o custo e reduzir o impacto ambiental. Porém, para cada tipo de obra há um ganho específico, como explica Cláudio Afonso Schmidt, gerente de equipamentos na Construtora Norberto Odebrecht. "Em obras habitacionais, a automação substitui a mão de obra. Já nas de infraestrutura, os ganhos ficam por conta das menores perdas e maior precisão na execução dos serviços, devido aos grandes volumes envolvidos", diz.
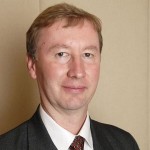
É o agronegócio quem inspira a construção civil a investir em "máquinas inteligentes". O setor agrícola já se preocupa com o aprimoramento de equipamentos desde o final do século passado. A ponto de importantes universidades brasileiras estarem ligadas a pesquisas nesta área. Uma delas é a USP (Universidade de São Paulo) com o LAA (Laboratório de Automação Agrícola) que existe desde 1989. O objetivo é aplicar a tecnologia da informação ao agronegócio. "Se analisarmos o que ocorreu no setor agrícola nas últimas décadas, diria que a construção civil está andando a passos lentos. Estes sistemas permitiram que os gestores do agronegócio tivessem informações em tempo real para a tomada de decisão", destaca Elson Rangel, líder da área de Pessoas, Organização e Engenharia da Odebrecht.
As recentes experiências com equipamentos totalmente ou parcialmente automatizados já permitiram às construtoras enumerar as seguintes vantagens:
• Redução no número de máquinas em operação, sejam os da própria empresa ou os alugados, devido à melhor utilização da frota
• Redução no consumo de combustível
• Uso correto dos equipamentos para cada tipo de trabalho
• Redução no desgaste e, consequentemente, no estoque de peças
• Melhoria da confiabilidade devido ao mapeamento das falhas redundantes
Para implantar inovações tecnológicas na área de gestão de equipamentos, as construtoras têm investido em sistemas de monitoramento interligado com ERPs, sistemas de controle de máquinas interligados com o planejamento da produção e uso de tecnologia móvel (GPS) para coleta de dados e integração com ERP. Há também a concentração de recursos em sistemas de monitoramento em tempo real das funções vitais da máquina, bem como ferramentas eletrônicas de diagnósticos, que permitem aos técnicos analisar falhas nos equipamentos. "A melhor gestão das máquinas aumenta a produtividade, pois diminui o retrabalho, eleva a precisão na execução dos serviços e reduz a influência de erros causados pelo fator humano", avalia Cláudio Afonso Schmidt.
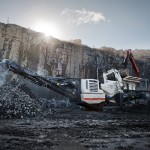
No canteiro de obras, hoje já é possível a automação de equipamentos como motoniveladoras com controle de nivelamento automático, rolos compactadores, pavimentadoras de asfalto e de concreto, além de plantas industriais com gestão automatizada de produção. "Existem casos em que a automação elimina completamente os operadores, como tem sido visto, com cada vez mais frequência, nas minas subterrâneas e em ferramentas de controle topográfico", completa o gerente de equipamentos da Odebrecht, reforçando que todo esse aparato tecnológico requer menos mão de obra, mas com mais qualificação. "Os operadores destas máquinas precisam de conhecimento técnico e para treiná-los é bastante comum o uso de simuladores de operação."
Os engenheiros da Odebrecht admitem que, apesar de todos os ganhos que a automação possa trazer à produtividade no canteiro de obras, não são todas as construtoras que estão investindo nesta área. Para eles, algumas esbarram nos custos e outras avaliam que a falta de maiores exigências técnicas na qualidade final dos serviços e produtos não estimula a busca de processos automatizados. Diferentemente do agronegócio, que, por causa da concorrência imposta por outros países, precisou se unir em torno da tecnologia e da inovação. "Neste ponto, o agronegócio é modelo para a construção civil", sinaliza Cláudio Afonso Schmidt.
Entrevistados
Engenheiro mecânico Cláudio Afonso Schmidt, gerente de equipamentos na Construtora Norberto Odebrecht e engenheiro civil Elson Rangel, líder da área de Pessoas, Organização e Engenharia da Odebrecht
Contato: mecanicca@terra.com.br
Créditos Fotos: Divulgação/Marcelo Vigneron
Jornalista responsável: Altair Santos MTB 2330
Jornal britânico elege 10 pontes mais bonitas do mundo
Relação do The Guardian inclui desde obras erguidas no século 12 até construções supermodernas, como a Viaduc de Millau, na França
Por: Altair Santos
O jornal britânico The Guardian listou em uma de suas últimas edições de 2013 as dez pontes que, segundo critérios definidos por jornalistas da publicação, podem ser consideradas as mais bonitas já construídas no mundo. Foram levadas em consideração opiniões de arquitetos e engenheiros civis, além dos desafios para construí-las. A relação inclui desde obras erguidas no século 12, como a Old London Bridge, demolida em 1831, até construções supermodernas, como a Millau Viaduct, na França, considerada a ponte mais alta do mundo. Cada uma das eleitas procurou retratar também a evolução da engenharia e do uso de sistemas construtivos.
As dez eleitas foram as seguintes:
1ª) Old London Bridge
Construídas com pedras, a velha ponte de Londres foi usada de 1176 a 1831, quando ocorreu sua demolição. Ela foi inspirada nas embarcações britânicas e sustentava, além de uma passarela que servia de travessia para pedestres e veículos de tração animal, edificações que eram habitadas normalmente por famílias de comerciantes londrinos.
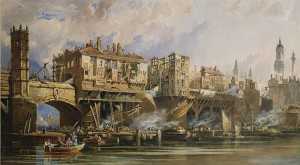
2ª) Pontes de raízes
Em Umshiang, no nordeste da Índia, em uma das regiões mais chuvosas do planeta, as pontes são construídas com raízes vivas de árvores. As estruturas podem durar centenas de anos e, apesar de simples, revelam uma engenhosidade que surpreendeu o jurado escolhido para eleger as pontes mais bonitas do mundo.
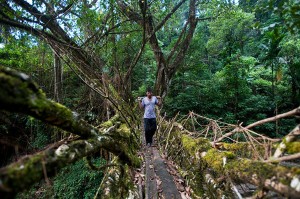
3ª) Viaduc de Millau
É considerada a ponte mais alta do mundo. Projetada pelo arquiteto inglês Norman Foster e pelo engenheiro francês Michel Virlogeux, tem 343 metros de altura. Foi inaugurada em 2004 e atravessa o rio Tarn, no sudoeste da França. A ponte é estaiada, mas sustentada por sete pilares que medem de 77 metros até 246 metros.
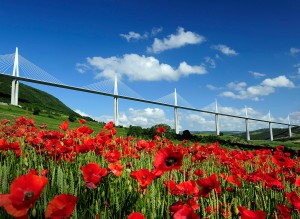
4ª) Punt Da Suransuns
Com um vão de 40 metros, a Punt Da Suransuns atravessa o rio Hinterrhein, na Suíça, e foi construída com placas de granito sustentadas por barras de aço. Exclusiva para pedestres, a ponte foi concluída em 1999 e localiza-se no desfiladeiro Viamala. Foi projetada pelo engenheiro Conzett Bronzini Gartmann.
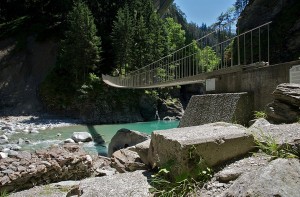
5ª) Ponte Salginatobel
Na Europa, o engenheiro suíço Robert Maillart é considerado um dos pioneiros em técnicas de construção em concreto armado. Por isso, a ponte Salginatobel é uma das obras de arte da engenharia do Velho Continente. Construída em 1930, na Suíça, ela tem um vão livre de 90 metros, sustentada por arcos triarticulados.
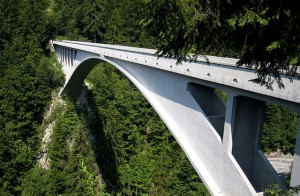
6ª) Bridge Burlington Northern
Sobre o rio Willamette, perto da cidade de Portland, no Oregon-EUA, a ponte foi construída em 1908 e serve para a travessia de trens. A obra conta com um mecanismo que permite que ela gire sobre um eixo, abrindo caminho para a navegação de grandes embarcações. Construída em aço, ela é sustentada por pilares de concreto armado. Funciona plenamente até hoje.
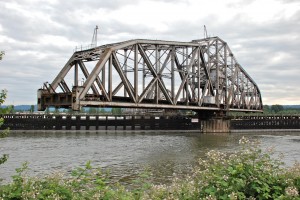
7ª) Ponte Maria Pia
Construída por Gustavo Eiffel, em 1877, a ponte Maria Pia cruza o Douro, na cidade do Porto, em Portugal, sem que haja pilares no leito do rio. Construída toda em estrutura de aço, a obra inspirou o engenheiro francês a projetar a Torre Eiffel, inaugurada em 1889. A Maria Pia conta com um tabuleiro de 352 metros de extensão e encontra-se a uma altura de 61 metros.
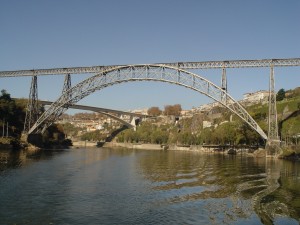
8ª) Nanpu Bridge
Construída em 1991, em Shangai, na China, a Nanpu Bridge é mais do que uma ponte estaiada. Inspirada em desenhos animados futuristas, como Os Jetsons, a obra tem um vão livre de 428 metros, que é acessado por quatro rampas circulares. Projetada pelo Instituto de Engenharia de Shangai, a ponte é considerada a 57ª maior ponte estaiada do mundo.
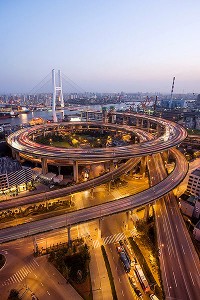
9ª) Aqueduto Pontcysyllte
Construída em 1805 no País de Gales, a ponte tem dupla função. Além de ser um aqueduto serve também de rota para o transporte fluvial de pequenas embarcações. Está construída sobre pilares de alvenaria e suas calhas de ferro fundido utilizam o curso d'água do Canal Llangollen. A obra tem 307 metros de comprimento e 38 metros de altura.
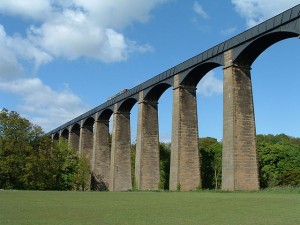
10ª) Khaju Bridge
Construída na província de Isfahan, por volta de 1650, quando o Irã ainda conhecido com Pérsia , a Jhaju Brigde foi eleita pela sua funcionalidade. Além de ponte, ela funciona também como uma eclusa. Suas galerias também abrigam as famosas casas de chá iranianas. A ponte, que funciona até hoje, tem pedras de grande porte como elementos estruturantes.
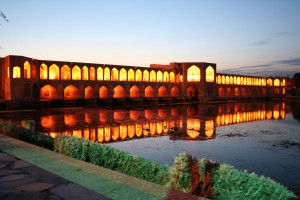
Crédito Foto: Divulgação
Jornalista responsável: Altair Santos MTB 2330
Arena das Dunas é o 7º estádio pronto para a Copa
Construção recuperou tempo perdido investindo em estruturas pré-fabricadas e foi o único que cumpriu com os prazos exigidos pela Fifa
Por: Altair Santos
Há um ano, o estádio Arena das Dunas - um dos 12 escolhidos para receber jogos da Copa do Mundo - era o que estava com as obras mais atrasadas. Com planejamento e investimento maciço nas tecnologias do concreto pré-fabricado e das estruturas metálicas, a obra de Natal conseguiu recuperar o cronograma e cumprir à risca o prazo dado pela Fifa. No dia 22 de janeiro de 2014, foi inaugurado com capacidade para receber 42 mil pessoas e investimento de R$ 423 milhões.
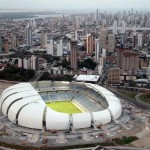
A Arena das Dunas tornou-se o 7º estádio a ficar pronto para a Copa do Mundo. Foi construído no mesmo terreno onde se encontrava o antigo estádio de Natal, conhecido como Machadão. A demolição desta obra, e de um ginásio anexo, resultou em 14 mil m³ de concreto reciclado, usado para construir peças pré-moldadas que foram empregadas em áreas não estruturantes da Arena das Dunas. No total, o novo estádio da capital potiguar consumiu 43 mil m³ de concreto.
Construída pelo consórcio OAS Coesa, a Arena das Dunas terá sua capacidade diminuída após a Copa do Mundo. O número de lugares cairá de 42 mil para 31.375. Seu projeto arquitetônico foi desenvolvido pela empresa norte-americana Populous, especializada em obras relacionadas com o esporte. A companhia também projetou os ginásios de Sochi, na Rússia, onde acontecem os jogos olímpicos de inverno, e atuará naquele país planejando alguns dos estádios que receberão partidas da Copa do Mundo de 2018.
No caso da Arena das Dunas, a Populous inovou na fachada do estádio, fazendo com que a cobertura imitasse pétalas que recobrem as arquibancadas. São 20 módulos que facilitam a ventilação e a penetração da luz natural dentro do estádio. As estruturas são feitas de treliças de aço, cobertas por telhas de alumínio, com isolamento térmico e acústico. Internamente, elas são revestidas com membranas de PVC pré-esforçado. As peças são unidas por policarbonato translúcido.
O telhado da Arena das Dunas também foi planejado para captar chuva. Calhas recolhem a água e levam-na para nove tanques abaixo das arquibancadas inferiores. Até 3 mil m³ podem ser capturados e reutilizados nos banheiros ou para irrigar o gramado. "O projeto da cobertura foi fundamental para que recuperássemos o tempo perdido e conseguíssemos entregar a obra dentro do prazo", diz o engenheiro civil Demétrio Paulo Torres, que ocupa o cargo de secretário extraordinário para assuntos relativos à Copa do Mundo de 2014, dentro do governo do Rio Grande do Norte.
Entrevistado
Engenheiro civil Demétrio Paulo Torres, secretário extraordinário para assuntos relativos à Copa do Mundo de 2014 - organismo ligado ao governo do Rio Grande do Norte
Contatos
secopa@rn.gov.br
secoparn@gmail.com
Crédito Foto: Canindé Soares/SecopaRN
Jornalista responsável: Altair Santos MTB 2330
Casa moldada "in loco" desencadeia franquia
Norma para paredes de concreto permite reconhecimento do sistema construtivo e sua adaptação para a produção em larga escala
Por: Altair Santos
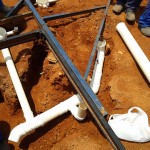
Publicada em maio de 2012, a ABNT NBR 16055:2012 (Parede de concreto moldada “in loco” para a construção de edificações - Requisitos e Procedimentos) tinha a intenção de popularizar a tecnologia. Agora reconhecido pelo Sistema Nacional de Aprovações Técnicas (Sinat), e com possibilidade de obter financiamento da Caixa Econômica Federal, o sistema construtivo ganhou o impulso de que precisava. A ponto de viabilizar a primeira franquia de construção de casas no Brasil. O modelo de concessão de venda permite erguer habitações em concreto moldado “in loco”, com fôrmas modulares de resina plástica. É assim que a Concre House já construiu 20 mil m² só no estado de São Paulo.
Para permitir que o sistema construtivo de paredes de concreto moldadas "in loco" fosse viável para o uso em franquias, o arquiteto Cláudio Barcellos, junto com a Universidade Sul– Riograndense, desenvolveu fôrmas modulares de resina plástica. Reutilizáveis, os equipamentos reduzem o risco de erro na montagem e geram menos entulhos e resíduos poluentes. Além disso, permitem redução de custo e suportam a aplicação de concreto com resistência final de 25 MPa, elaborado especificamente para a aplicação nas fôrmas. "Um sobrado de 60 m² utiliza 29 m³ de concreto, incluindo a fundação radier, paredes e lajes", explica Cláudio Barcellos.

Uma casa da franquia é erguida em duas semanas e finalizada em cinco semanas. Toda a tubulação elétrica e hidráulica é embutida no processo construtivo. Após a retirada das fôrmas, a construção fica com um aspecto monolítico de concreto, podendo receber acabamento final com textura colorida ou massa fina internamente e externamente nas paredes e no teto, e com cerâmicas nas áreas frias. A Concre House fiscaliza seus franqueados através de um software de gestão de obras e do acompanhamento de consultores de campo. Além disso, há o suporte de uma equipe de engenheiros civis. Atualmente, a franquia atua apenas em São Paulo. Em 2014, a meta é abrir dez unidades em outros estados.
Para se associar à Concre House, o franqueado precisa de um investimento mínimo de R$ 230 mil. O empreendedor não necessita ser graduado em engenharia civil, mas exige-se que tenha técnicos em edificação em seu quadro de funcionários. Além disso, ele recebe manuais de procedimento e os kits para a construção das casas. As ARTs (Anotações de Responsabilidade Técnica) são assinadas por engenheiros civis contratados pela franquia, assim como o acompanhamento da obra. "A franquia dá todo o suporte de engenharia", afirma Cláudio Barcellos.
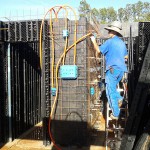
A construção das casas passam por sete etapas:
1) Montagem de gabarito, abertura e fechamento de esgoto e efluentes, com colocação de caixas de inspeção.
2) Concretagem do radier e execução de contrapiso.
3) Marcação, montagem de kits e dos elementos elétricos e hidráulicos dentro das fôrmas, além de concretagem e desmontagem das fôrmas de paredes e lajes.
4) Montagem da estrutura do telhado, colocação de telhas e acabamento elétrico.
5) Colocação dos revestimentos: massa lisa, piso cerâmico, rodapé cerâmico, azulejos, textura externa e forros em gesso.
6) Colocação de esquadrias, louças e metais.
7) Pintura interna e externa.

Entrevistado
Arquiteto Cláudio Barcellos, idealizador do sistema construtivo usado pela Concre House.
Contato: contato@concrehouse.com.br
Créditos Fotos: Divulgação/Concre House
Jornalista responsável: Altair Santos MTB 2330
Pesquisa global busca cimento de baixo carbono
Poli-USP faz parte de estudo que tenta reduzir emissão de CO₂, mas normalização no Brasil precisa permitir adição em teores mais elevados
Por: Altair Santos
Em abril de 2013, os professores da Poli-USP, Vanderley John e Rafael Pileggi, apresentaram os resultados de uma pesquisa que resultou em produção de cimento com menor emissão de CO₂. Os estudos também mostraram que é possível, através do controle, da seleção e da combinação das matérias-primas usadas para produzir o cimento, aumentar a produtividade sem precisar consumir mais energia, equipamentos e mão de obra.
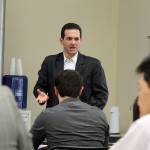
Atualmente a norma para a fabricação do cimento tipo CP III – Cimento Portland de alto-forno permite a adição de até 70% de escória granulada de alto-forno mais 5% de fíler calcário ou outro material carbonático, com 25% de clínquer mais gesso. Já no cimento tipo CP IV – Cimento Portland pozolânico a adição permitida é de até 50% de material pozolânico mais 5% de fíler calcário, com 45% de clínquer mais gesso. Para os cimentos tipo CP II – Cimento Portland composto, a adição de fíler permitida é de até 10%.
Os testes hoje integram uma cadeia global de pesquisadores, que persegue a produção em escala industrial do Low Carbon Cement (LCC) ou cimento de baixo carbono. O Brasil, que tem a indústria cimenteira mais ecoeficiente do mundo, está entre os líderes da pesquisa. É o que explica o professor doutor Rafael Pileggi, do departamento de engenharia de construção civil da Escola Politécnica da Universidade de São Paulo. Confira a entrevista:
Em 2013, o departamento em que o senhor atua na Escola Politécnica (Poli) da USP (Universidade de São Paulo) apresentou o resultado de uma pesquisa que reduz a emissão de CO₂ na fabricação de cimento. Os estudos tiveram mais avanços de lá para cá?
A linha de nossa pesquisa é produzir cimento Portland com menor teor de clinquer, substituindo parte deste material, que é o que mais emite CO₂ na fabricação de cimento, por materiais cimentícios suplementares - também conhecidos como fillers. Temos utilizado fillers calcários e outros fillers que não passam por processamento industrial. Seguimos trabalhando nesta pesquisa, só que ela ainda está restrita ao campo universitário, pois o cimento, para ir ao mercado, depende de normalização e as normas brasileiras de cimento definem teores bastante baixos de fillers. Do ponto de vista da pesquisa, obtivemos mais avanços. Mas do ponto de vista de normalização, o resultado da pesquisa ainda não pode ser colocado no mercado.
Aumentar o volume de fillers na fórmula do cimento Portland não afeta a qualidade do material?
Não, porque não é qualquer filler. Tem que ser um filler com características e partículas de tamanhos adequados. Quando o filler - nome de fantasia para o pó fino que é colocado junto ao cimento -, não é controlado o tamanho destas partículas podem prejudicar a propriedade. Mas colocadas em quantidades e tamanhos certos, eles melhoram muito a propriedade e melhoram o efeito de empacotamento de partículas. O sistema fica melhor empacotado. Então, é possível fazer cimento muito mais forte se ele tiver menos do cimento reativo e uma fração de granometria bem adequada para o produto final. Para se ter uma ideia, conseguimos fazer concreto com 1/4 do teor de cimento e com a mesma resistência. Ganhamos um concurso na Suécia, há dois anos, por produzir concreto ecoeficiente com 190 quilos de cimento e que atingiu quase 90 megapascal de resistência. Um concreto deste, para atingir esta resistência, normalmente é feito com 800 quilos de cimento. Em outro ensaio, fizemos concreto com 120 quilos de cimento e obtivemos 50 megapascal, que no mercado brasileiro é conseguido com 400 quilos. Concreto de 40 megapascal, fizemos com 80 quilos de cimento. Então, do ponto de vista da resistência mecânica, se for usado o filler certo, na quantidade certa, junto com aditivos superfortificantes adequados, é possível ganhar em propriedades. Esta é a essência da pesquisa, que está evoluindo. Em contrapartida, tem uma questão de normalização que define o teor máximo de filler. No Brasil, não pode passar de 10% (Cimento Portland composto) e estamos falando, no futuro, de cimentos que tenham 30% de clinquer e 70% de filler. A curto prazo não existe legislação que permita isso, por que ainda é preciso que se estude bastante os aspectos ligados a durabilidade. Como esta é uma pesquisa crescente no mundo inteiro, e no Brasil lideramos com o filler calcário, fazemos parte de uma rede internacional europeia que trabalha com filler e outros tipos de adições. Este grupo internacional estuda os aspectos ligados à durabilidade e com certeza ninguém vai mudar do dia para a noite. Mas o objetivo é fazer cair relativamente o teor de clinquer. Com isso, se consegue aumentar a produção total de cimento sem aumentar o número de fornos. O ideal é que a indústria cimenteira dobre a produção com os fornos que têm hoje. É nesta estratégia que nós estamos trabalhando.
A pesquisa também mostrou que é possível reduzir a emissão e aumentar a produtividade, melhorando o controle, a seleção e a combinação das matérias-primas. De que forma?
Existe um conceito neste tipo de material que é o conceito de empacotamento de partículas. A partícula do cimento, hoje, tem duas funções quando reage com a água e endurece. Uma é ocupar espaço e a outra é colar na partícula vizinha. Na pesquisa, para esta função de ocupar o espaço usamos outras partículas. O cimento passou a ter somente a função de colar as partículas. Quando se faz isso, obtém-se a mesma performance com um teor de cimento menor e o cimento passa ser usado naquilo em que ele é nobre: ser reativo e aderir na partícula vizinha. Ocupar espaço, esta função de enchimento, quem passa a fazer são estas outras partículas de matérias-primas como calcário, sílica e argilas. Estamos trabalhando fortemente com calcário, que é a matéria-prima mais abundante. Então, no mundo do futuro, como vai ser a fábrica de cimento? Haverá os mesmos formos, mas diferentes moinhos. Um moinho moendo clinquer, um moinho moendo um filler A e outro moinho moendo um filler B. Lá na frente haverá a combinação nas proporções adequadas para fabricar cimento com determinada tipologia. Esta não é uma estratégia não testada. A indústria de concreto refratário já passou por isso. Tanto que existem materiais de concreto refratário feitos com menos de 2% de cimento e eles são muito resistentes. O que eles têm de diferente é a questão de durabilidade. Como eles vão para um forno, ela reage pelo forno, nós não temos o forno aqui, mas o início é igual para os dois. Então realmente o que se discute hoje é durabilidade.
Mas já não existem outras estratégias para se reduzir o impacto ambiental da produção de cimento e da emissão de CO₂?
Sim, mas o problema é que são extremamente caras. Uma delas seria pegar o CO₂ que sai da chaminé de cimento e enterrar. Se for feito isso em escala global isso dobraria o custo do cimento. Outra é aproveitar escórias de alto forno. O problema é que esses materiais não existem em quantidade suficiente. Enquanto o Brasil produz 70 milhões de toneladas de cimento por ano, a escória não passa de 10 milhões de toneladas. Isso obriga que se desenvolva uma tecnologia que permita diluir o clinquer, que possibilite substituí-lo por outro material na granometria adequada. Nós conseguimos produzir um cimento com características parecidas, sem mexer no parque industrial estabelecido, sobretudo nos fornos. A fábrica vai poder fazer cimento com menor produção de clinquer por quilo de cimento, resultando em um impacto ambiental menor e em um custo final compatível aos custos de hoje.
O cimento produzido na pesquisa foi testado apenas na produção de concreto?
No concreto, na argamassa e no fibrocimento. Em todos os casos obtivemos a mesma propriedade de um produto convencional, mas com a metade do teor de clinquer.
Como a indústria cimenteira recebe a pesquisa?
Recebeu muito positivamente porque a indústria tem uma necessidade urgente em dar uma resposta à sociedade na questão da emissão de CO₂. A indústria cimenteira responde hoje por 6% da emissão de CO₂. Em qualquer cenário de crescimento, ela pode evoluir em 15 anos para 20% de CO₂, ou seja, a indústria cimenteira sabe que precisa reduzir o impacto da emissão de CO₂. Todas as indústrias estão fazendo isso. É uma tendência.
A pesquisa realizada na Poli chegou a ser levada para fora do país?
Existem grupos lá fora que trabalham de maneira equivalente no assunto e participamos agora de uma rede de pesquisa junto com a comunidade europeia. Este cimento com menor teor de clinquer já recebeu a denominação de cimento de baixo carbono, em inglês LCC (Low Carbon Cement). As pesquisas em Low Carbon Cement são pesquisas mundiais, com grupos internacionais, juntados em uma rede para troca de experiências. Nós fazemos parte desta rede.
Como o senhor vê a ecoeficiência da indústria cimenteira no Brasil, comparada com outros países?
O Brasil produz o cimento mais ecoeficiente do mundo. O conceito da norma do cimento CP III brasileiro é um cimento de baixo impacto ambiental, por que é 25% clinquer, 5% de gesso e 70% de escória. Esta ideia é que está ganhando derivações: fazer um produto com matéria-prima que tenha em abundância no mundo inteiro. Essa matéria-prima são os fillers calcários ou argilas calcinadas. Com eles, poderíamos ter todo o cimento do mundo com 30% de clinquer. Mas sobre este aspecto, o Brasil é pioneiro e é reconhecido no mundo como um cimento de baixo impacto.
Entrevistado
Engenheiro civil e professor doutor do departamento de engenharia de construção civil da Escola Politécnica da Universidade de São Paulo, Rafael Giuliano Pileggi.
Contato: rafael.pileggi@poli.usp.br
Crédito Foto: Marcos Santos/USP Imagens
Jornalista responsável: Altair Santos MTB 2330
Concreto polido: do chão da fábrica à decoração
Piso ganha interior das casas, mas é preciso o emprego adequado de tecnologias e de elementos agregados para se evitar patologias
Por: Altair Santos
O piso de concreto polido tornou-se elemento de decoração em residências de alto padrão construídas nas cidades de Los Angeles e Miami, nos Estados Unidos. Seguindo a tendência, passou a ser usado no Brasil com a mesma finalidade de acabamento interior. Antes limitado ao chão da fábrica, o material invadiu a sala de estar, os quartos e a cozinha, graças a tecnologias como o polimento por diamante e novos reagentes agregados ao concreto. Entre eles, endurecedores de superfície à base de nanosílica, silicato de sódio, flúor silicato ou impregnantes poliméricos com resina epoxy.
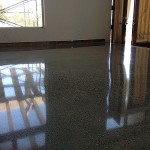
Por isso, o emprego do concreto polido em superfícies internas de residências requer a contratação de empresas especializadas. Seu uso, por exemplo, impõe restrições ao cimento Portland CP III, devido à presença de escórias e pozolanas. Já a resistência mínima à compressão deve ser de 35 MPa. Além disso, para se ganhar brilho no processo de polimento deve-se aumentar a dureza da superfície em até 6 ou 7 Mohs - a escala de Mohs quantifica a dureza dos minerais. Já os agregados do concreto, desde que o cliente deseje um polimento mais profundo, a opção deve ser por materiais mais decorativos.
Outro detalhe importante é que o lançamento do concreto precisa ser sempre agendado para os primeiros horários da manhã. É recomendável informar a concreteira que será aplicado um concreto com "traço para piso acabado" ou "traço para piso polido". Esse concreto vem com menor ou nenhuma quantidade de retardador de pega, fundamental para o uso em pisos polidos. Todos esses cuidados são para evitar uma das patologias mais comuns a esse tipo de piso: o lascamento ou delaminação. Normalmente, ela ocorre por causa do polimento prematuro ou do emprego de um concreto inadequado.
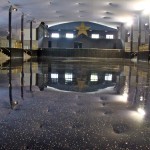
Para evitá-la, é preciso fazer o polimento após encerrado o processo de exudação do concreto, a fim de que não se criem lâminas d'água abaixo da superfície. Outra recomendação importante está na manutenção do piso. De preferência, ela deve ser sempre a seco, ficando proibido o uso de produtos ácidos, como "lava pedras". Bem aplicado, o piso de concreto polido apresenta pelo menos seis vantagens em relação a outros revestimentos. São elas:
1) Vida útil muito mais longa do que cerâmicas, madeiras ou carpetes.
2) Fácil manutenção.
3) Redução substancial na proliferação de mofos, ácaros e bactérias. Por isso é recomendável como piso interior para pessoas alérgicas e portadoras de doenças respiratórias.
4) Adapta-se a qualquer tipo de decoração.
5) Custo mais barato do que pisos que recebem placas de mármore ou granito.
6) Propiciam eficiência energética, pois o brilho reflete tanto calor quanto luz.
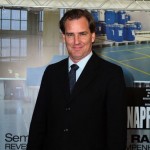
Entrevistado
Engenheiro mecânico Alexis Joseph Steverlynck Fonteyne, vice-presidente da ANAPRE (Associação Nacional de Pisos e Revestimentos de Alto Desempenho) e sócio-proprietário da Solepoxy Indústria e Comércio de Resinas - empresa fabricante de produtos e sistemas para revestimentos de alto desempenho.
Contato: anapre@anapre.org.br
Créditos Fotos: Divulgação/ANAPRE/Solepoxy
Jornalista responsável: Altair Santos MTB 2330
Há 20 anos, uma nova construção civil nascia no país
Plano Real, lançado em 1994, teve o mérito de fazer com que produtos do setor, como materiais e habitações, coubessem no bolso do consumidor
Por: Altair Santos
O Plano Real completa 20 anos em 2014. Em fevereiro daquele ano foi dado o primeiro passo do programa de estabilização monetária que, ao longo de duas décadas, permitiu que entrasse em cena uma nova classe de consumidores. São esses cidadãos que vieram a lotar aeroportos, passaram a adquirir veículos populares, deram números astronômicos à venda de aparelhos celulares, transformaram o varejo de material de construção e fizeram nascer programas como o Minha Casa Minha Vida.
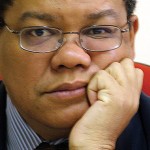
Estima-se que o poder de compra desta chamada nova classe C chegue hoje a 600 bilhões de dólares por ano - aproximadamente R$ 1,45 trilhão. Ela fez nascer um índice denominado de Poder de Compra do Consumidor Popular (PCCP) o qual baliza vários setores da economia nacional, incluindo o da cadeia produtiva da construção civil. Até 2016, a influência destes consumidores estará ainda maior. Estima-se que representarão, daqui a dois anos, 75% de toda a população com poder de compra no país.
Seriam 90 milhões de brasileiros. E, segundo Marco Roza, diretor da Agência Consumidor Popular, os setores da economia que melhor têm se conectado a esses consumidores são aqueles que criaram uma interface financeira para seus produtos. "São os setores que conseguiram embutir juros a conta-gotas nas prestações cobradas por suas mercadorias. Por exemplo, móveis, eletrodomésticos, materiais de construção, sapatos, roupas, automóveis e motocicletas. Ao “financeirizar” as prestações, grandes redes passaram a atender às necessidades represadas desses consumidores fazendo com que as prestações, mesmo com os juros embutidos, coubessem em seus bolsos", explica.
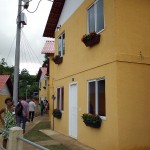
Especificamente sobre o setor da construção civil voltado ao varejo, Marco Roza destaca que quem melhor se adaptou foram as grandes distribuidoras de material de construção e de acabamento, que atraíram os consumidores através de oferta direta de crédito e ajuste das prestações aos bolsos dos clientes e donos de imóveis populares. Porém, ele ressalta que falta isso chegar com mais intensidade ao Minha Casa Minha Vida. Motivo: as grandes construtoras do país não se interessaram pela chamada faixa 1 do programa, deixando esse segmento apenas para pequenas construtoras e para o poder público (Cohabs). "Isso impede uma escala produtiva que atenda as necessidades represadas e a pressa dos consumidores populares", avalia.
A alternativa encontrada pelo cidadão que deveria ser beneficiado pela faixa 1 do MCMV foi aderir ao comércio formiguinha (compra mensal de pequenos volumes de material de construção) para transformar barracos de favelas em casas de alvenaria. "O comércio formiguinha deveria se transformar em alerta máximo para as imensas oportunidades que existem para a construção civil neste segmento de consumo. Normalmente, o comércio formiguinha paga uma taxa extra de acesso aos produtos. É um pedágio que poderia ser eliminado ou dividido entre as partes, se as construtoras começassem a investir no relacionamento direto com esses consumidores populares", finaliza Marco Roza.
Entrevistado
Marco Roza, diretor da Agência Consumidor Popular
Contato: marcoroza@mdm.com.br
Créditos Fotos: Divulgação/Paulo Bastos/Prefeitura do Rio
Jornalista responsável: Altair Santos MTB 2330
Rodovias do futuro tendem a unir concreto e asfalto
Conferência debate novos conceitos e aplicações de tecnologias mistas para as estradas federais, a partir das concessões que têm sido viabilizadas
Por: Altair Santos
Desde que a Confederação Nacional do Transporte (CNT) passou a divulgar pesquisas sobre o estado das rodovias federais no Brasil, a constatação é uma só: a cada nova rodada do levantamento pioram as condições das estradas. Nos dados mais recentes, que constam na 17ª edição do estudo, de 96.714 quilômetros avaliados 63,8% apresentaram alguma deficiência no pavimento, na sinalização ou na geometria da via. Em 2012, o índice havia sido de 62,7%. Salvam-se os 15.873 quilômetros já em regime de concessão ou que já operam cobrando pedágio. Nestes trechos é que começa a ser testado um novo tipo de rodovia: a que procura alternar trechos de asfalto com pavimento de concreto ou une os dois materiais no mesmo percurso.
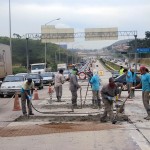
A experiência foi relatada na conferência Rodovias do Futuro, realizada no final de janeiro de 2014, em São Paulo. O encontro reuniu as áreas de engenharia das empresas que operam as estradas sob regime de concessão, onde foram mostrados exemplos em que o tráfego mais intenso de veículos pesados obrigou a construção de um corredor de pavimento rígido ao lado de um corredor de asfalto. O modelo segue tendência que já é comum nas áreas urbanas, principalmente nas vias onde circulam linhas exclusivas de BRT (Bus Rapid Transit). "Hoje, para as empresas que operam as concessões, a escolha do tipo de pavimentação é uma das questões mais relevantes no planejamento das rodovias", comentou o presidente do Instituto Pavimentar, Rafael Marçal Martins de Reis.
Uma das tecnologias que permite agregar pavimento rígido ao asfalto é conhecida como whitetopping (WT). Trata-se da técnica de reabilitação de pavimentos com revestimento asfáltico (flexíveis, invertidos ou semirrígidos) em que o pavimento de concreto é aplicado diretamente sobre eles, com ou sem camadas de nivelamento, conforme os procedimentos clássicos de projeto e construção dos pavimentos rígidos. Atualmente, a engenharia rodoviária possui três tipos de WT: 1) Tradicional, com espessura mínima de até 10 centímetros que pode ser aplicado em qualquer estado de degradação do pavimento flexível; 2) Ultradelgado, com espessuras entre 10 centímetros a 5 centímetros, que se presta para reforçar estruturalmente o pavimento existente; 3) Delgado composto, que é uma estrutura que mescla vantajosamente as características dos dois primeiros tipos, permitindo espessuras entre as que resultariam entre a do WT tradicional e a do ultradelgado.
A coordenadora do centro de pesquisas rodoviárias da Concessionária NovaDutra, Valéria Cristina Faria, ressaltou que a execução do pavimento rígido é decisiva para seu sucesso, a fim de que ele dispense custos elevados de manutenção. "As técnicas de manutenção dos pavimentos rígidos são mais difíceis de serem executadas, se levarmos em consideração a demora no tempo de cura do concreto. Hoje existem materiais de pega rápida, porém apresentam um custo elevadíssimo. Há também as restrições operacionais que nos obrigam a executar tais reparos somente no período noturno, com janela de trabalho da meia-noite às 5h. Então, nossos cálculos sempre se baseiam na relação volume de tráfego versus período para execução dos trabalhos de manutenção", explica. A CCR NovaDutra utiliza pavimento de concreto no trecho que passa pela cidade de Guarulhos, na região metropolitana de São Paulo.
Entrevistados
- Valéria Cristina Faria, coordenadora do centro de pesquisas rodoviárias da Concessionária NovaDutra
- Rafael Marçal Martins de Reis, presidente do Instituto Pavimentar
Contatos
valeria.faria@grupoccr.com.br
contato@institutopavimentar.com.br
Crédito Foto: Divulgação
Jornalista responsável: Altair Santos MTB 2330
Indústria do shopping mira cidades de médio porte
Municípios de 300 mil a 200 mil habitantes tornam-se prioridade de construtoras e incorporadoras especializadas em erguer centros comerciais
Por: Altair Santos
Construtoras e incorporadoras especializadas em erguer shopping centers iniciam 2014 com uma nova prioridade: disputar as cidades entre 200 mil e 300 mil habitantes espalhadas pelo país. Estudos revelam que boa parte dos municípios deste porte no Brasil não tem centros de compra como os que são facilmente encontrados nas capitais. "A tendência do setor é suprir essa demanda, buscando a entrada em cidades menores, que tenham uma quantidade pequena de shopping ou que não sejam atendidas por shoppings centers", diz Luiz Alberto Marinho, sócio-diretor da GS&BW, empresa de consultoria especializada em estratégias para shopping centers.
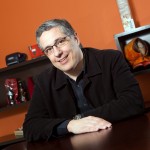
Dados da Associação Brasileira de Shoppings Centers (Abrasce) confirmam esse posicionamento do mercado. Em 2014 estão previstas 41 inaugurações de centro comerciais, dos quais 30 localizam-se fora das capitais, em cidade com população variando entre 200 mil a 500 mil habitantes. No país há 495 empreendimentos funcionando, dos quais 249 em 25 capitais e no Distrito Federal - exceto Boa Vista, em Roraima. O número é considerado baixo pelos especialistas, o que significa dizer que há espaço, inclusive, para que esse tipo de construção continue se expandindo em grandes metrópoles. "Desde que não haja sobreposição entre as áreas de influência, há muito espaço para crescer", avalia Luiz Alberto Marinho.
Os estudos de sobreposição são calculados pelo Ibope. Se um determinado índice der menor que 100, significa que na região do novo empreendimento já existem outros shopping centers e que pode não haver demanda suficiente. Outro parâmetro é a Área Bruta Locável (ABL) que é a área do empreendimento disponível para as lojas. "O Brasil ainda possui um média muito baixa de ABL. A nossa média está em torno de 50 m² para cada mil habitantes e isso é 1/3 do que acontece no México. Então existe ainda muito, mas muito espaço para novos shoppings centers. O que tem que tomar cuidado é para que não haja centros comerciais muito próximos, ou seja, que as áreas de influência tenham superposição", cita o sócio-diretor da GS&BW.
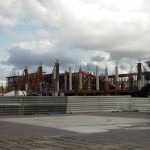
O potencial do Brasil para receber shopping centers já atraiu, entre 2008 e 2011, os principais players do mercado mundial do setor. "Eles chegaram ao país em associação com outras empresas. É importante lembrar que nós ainda não temos nem 500 shoppings no Brasil e nos Estados Unidos são mais de 40 mil", alerta Luiz Alberto Marinho, para quem as empresas especializadas em construção de centros comerciais tendem a seguir fazendo bons negócios. "O modelo dos shopping centers baseado no aluguel, nas lojas, na cessão de direitos, nas luvas, é bastante interessante. Some-se a isso, o consumo de varejo, que segue em alta. É uma conjunção que fez com que o negócio continue bastante lucrativo", finaliza.
Entrevistado
Luiz Alberto Marinho, professor do núcleo de varejo da ESPM – Escola Superior de Propaganda e Marketing; instrutor do International Council of Shopping Centers, e sócio-diretor da GS&BW, empresa de consultoria especializada em estratégias para shopping centers
Contato: atendimento@gsbw.com.br
Crédito Fotos: Divulgação/ GS&BW