Tufão testa, e aprova, amortecedor mais famoso do mundo
Fenômeno com ventos de até 210 km/h atingiu o edifício Taipei 101, em agosto de 2015, e esfera de aço de 720 toneladas neutralizou risco de danos
Por: Altair Santos
O Taipei 101, inaugurado em 1999 na capital de Taiwan, é um dos edifícios que mais desperta a curiosidade de engenheiros e projetistas em todo o mundo. Motivo: o amortecedor de massa instalado no prédio é totalmente inovador. Para neutralizar o balanço causado por fortes ventos - típico do clima da região -, e eventuais terremotos, o projeto do arranha-céu de 508 metros de altura previu a instalação de uma enorme esfera de aço de 720 toneladas, localizada no núcleo da edificação - entre o 87º e 92º andares. O objetivo é compensar as forças externas que busquem inclinar o Taipei 101.
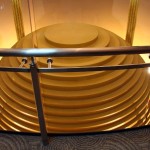
A peça sempre atraiu visitas técnicas de delegações de vários países, mas agora tem chamado ainda mais a atenção. No começo de agosto, a estrutura comprovou sua eficácia ao anular os efeitos do tufão Soudelor. O fenômeno passou por Taiwan com ventos de 210 km/h, e o edifício estava em sua rota. No entanto, o arranha-céu manteve-se intacto, pois o amortecedor cumpriu a função de compensar as forças externas, empurrando o prédio na direção contrária à do vento. O deslocamento da esfera, superior a 90 centímetros, manteve o edifício em posição estática.
O Taipei 101 também já passou no teste dos terremotos. Em 2002, um tremor de 6,8 graus na escala Richter balançou a edificação, mas os danos foram minimizados pelo amortecedor de massa. Em 2008, o tremor foi mais suave: 5 graus. Todos deixaram o prédio ileso, porque o arranha-céu foi projetado para suportar terremotos de até 7 graus e ventos com velocidade superior a 450 km/h. As dimensões do amortecedor de massa foram concebidas para atender essas especificações e também para se adequar ao peso do Taipei 101, que até 2004 foi o prédio mais alto do mundo.
Construído com estrutura mista de concreto e vigas de aço, o arranha-céu pesa 700.000 toneladas. Assentado sobre uma falha geológica, o Taipei 101 foi projetado pelo arquiteto e engenheiro chinês C. P. Wang, que o concebeu inspirado no bambu. A planta é conhecida pela sua capacidade de envergar sem quebrar. Seu segredo está nas seções ocas, articuladas por pequenos tubos. Seguindo essa lógica, o edifício possui treliças horizontais gigantes, armadas a cada oito andares. Essas estruturas, combinadas com o amortecedor de massa, dão ao edifício a flexibilidade necessária para suportar ventos e tremores.
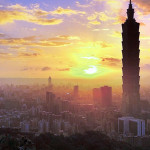
Informações técnicas do Taipei 101
Arquitetura e projeto: CYLee & Partners
Engenheiro estrutural : Shaw Shieh
Altura: 508 metros
Andares: 101
Desempenho do concreto: 70 MPa
Peso do amortecedor de massa: 720 toneladas
Quantidade de aço: 106 mil toneladas
Quantidade de concreto: 41 mil m³ (23 mil m³ só para o radier e os 382 pilares com 1,5 metro de diâmetro cada um, que estão fincados a 60 metros de profundidade)
Veja vídeo de como funciona o amortecedor de massa do Taipei 101:
Entrevistado
Escritório de arquitetura C.Y. Lee & Partners, Architects & Planners (via assessoria de imprensa)
Contato: info@mail.cylee.com
Créditos Fotos: Divulgação
Jornalista responsável: Altair Santos MTB 2330
Trem inglês de 465 metros vira central de concreto
Composição percorre trechos da Crossrail, em Londres, e entrega 50 mil m³ do material em novas etapas da obra, além de peças pré-fabricadas
Por: Altair Santos
A maior obra de mobilidade urbana da Europa está em andamento na cidade de Londres, na Inglaterra, e será entregue em 2018. Trata-se da Crossrail, uma linha férrea com 108 quilômetros de extensão, que ligará os lados leste e oeste da capital inglesa, unindo cidades da região metropolitana ao metrô londrino. O sistema tem 40 estações e 21 quilômetros subterrâneos. As composições irão correr sobre trilhos assentados em um radier de concreto. Para agilizar a construção, uma composição férrea de 465 metros foi transformada em uma central de concreto.
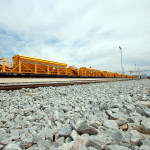
O trem possui capacidade de carregar agregados para produzir até 50 mil m³ de concreto e percorre os trechos prontos da ferrovia, entregando o material para as etapas a serem construídas. Nele há vagões carregados com cimento, pedra brita, areia e água, ou seja, todos os produtos necessários para a fabricação de um concreto resistente para o radier. “O trem-concreteira é o centro nervoso de nossa logística. Com ele, estamos mantendo nosso cronograma em dia”, afirma Simon Wright, engenheiro-chefe do projeto Crossrail. A obra está prevista para ser finalizada no primeiro semestre de 2018.
O trem-concreteira tem sido usado em um trecho de 40 quilômetros dos 108 que envolvem a obra. Além de produzir e distribuir o concreto, a composição serve também para transportar as peças pré-fabricadas para o revestimento dos túneis. São 250 mil elementos e parte também chega ao local da obra através de transporte fluvial. As peças são fabricadas em uma unidade montada exclusivamente para atender a Crossrail. Ela opera cinco dias por semana, 24 horas por dia. Há segmentos que chegam a pesar até 3,5 toneladas. São esses elementos mais pesados que têm sido transportados por embarcações.
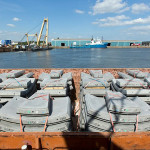
Obra para 120 anos
Segundo o consórcio encarregado pela obra, formado pelas empresas Alstom, TSO e Costain Limited, foram economizadas 10 mil viagens de caminhões com a opção pelo transporte fluvial e ferroviário, usando o trem-concreteira. “A autoridade portuária de Londres nos deu uma grande colaboração, orientando como transportar os pré-fabricados pelo rio Tâmisa”, explica James Trimmer, diretor de planejamento e meio ambiente do consórcio construtor. Com essas práticas de sustentabilidade, os especialistas envolvidos na construção da Crossrail calculam que a megaobra será concluída gastando 25% a menos de recursos naturais.
As obras da Crossrail começaram em 2009. Trata-se da maior obra de transporte urbano de Londres, desde a criação da primeira linha de metrô na cidade, em 1863. O empreendimento foi pensado para também incrementar a economia da cidade, gerando empregos para toda a cadeia produtiva da construção civil britânica. Quando pronta, a linha férrea terá a capacidade de acrescentar mais 1,5 milhão de pessoas ao sistema de transporte público de Londres. A obra foi idealizada para suportar o crescimento de Londres e de sua região metropolitana nos próximos 120 anos. O custo estimado é de 14,8 bilhões de libras (aproximadamente R$ 81,5 bilhões).
Veja vídeo sobre a Crossrail
https://youtu.be/kmRC0YIIaS4
Entrevistado
Consórcio construtor da Crossrail (via assessoria de imprensa)
Contato: pressoffice@crossrail.co.uk
Créditos Fotos: Divulgação/Crossrail
Jornalista responsável: Altair Santos MTB 2330
Saiba como vistoriar o imóvel novo e evite transtornos
Check list deve ser minucioso e, depois de detectados os vícios aparentes da obra, construtora tem, no máximo, 90 dias para consertá-los
Por: Altair Santos
Vistoriar o imóvel novo (casa ou apartamento) é uma exigência legal. A construtora só pode liberar as chaves se o proprietário concordar com o que viu na obra. O momento exige que o futuro dono se dispa de qualquer empolgação. Tendo em mãos o memorial descritivo entregue pelo construtor, o futuro morador precisa fazer um check-list minucioso. Deve ir desde a inspeção de portas e janelas até a instalação dos acabamentos, da pintura, do contrapiso, da hidráulica e da elétrica. Verificar erros construtivos e exigir o cumprimento de reparos antes da mudança evita transtornos e uma moradia segura.
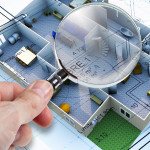
Na média nacional, desacordos na entrega do imóvel variam entre 30% e 40%. Para Marco Aurélio Luz, presidente da AMSPA (Associação dos Mutuários de São Paulo e Adjacências), a qualidade duvidosa dos materiais, combinada com mão de obra mal treinada, está entre os fatores que levam a erros construtivos. “Isso causa a maioria das patologias encontradas em vistorias: infiltrações e rachaduras, principalmente. Mas há também os desacordos em relação ao memorial descritivo, como a falta de pisos e de cerâmicas e porcelanatos que não condizem com o prometido, e também falhas na pintura”, explica.
É consenso, não só entre as associações de mutuários, mas principalmente entre as construtoras, que a Norma de Desempenho (ABNT NBR 15575) tende a minimizar desacordos construtivos, que, quando graves, podem levar até ao distrato da compra do imóvel. Marco Aurélio Luz, afirma que, legalmente, quando o comprador detecta problemas, a construtora tem prazo de 90 dias para corrigir os vícios aparentes. “Mesmo que o comprador aceite as chaves, ele precisa notificar a construtora e exigir os reparos. Principalmente se, no decorrer do uso do imóvel, surgirem os chamados vícios ocultos”, alerta o presidente da AMSPA.
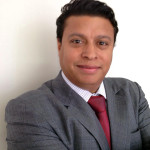
Quando ir à Justiça
O Código do Consumidor afirma que os compradores de imóveis têm garantia de 5 anos dada pelas construtoras, mas há decisões judiciais que estendem esse prazo para 20 anos, desde que os defeitos envolvam as estruturas da unidade. Caso a construtora não realize a reforma, o comprador precisa notificá-la formalmente e, preferencialmente, contratar um engenheiro para fazer um laudo com todos os problemas encontrados. Em seguida, requerer judicialmente os reparos. “O cumprimento dos reparos depende muito de construtora para construtora, mas a Norma de Desempenho tende a uniformizar isso”, avalia Marco Aurélio Luz.
A AMSPA tem uma cartilha que orienta o consumidor a vistoriar o imóvel, destacando os principais pontos a serem observados. Mas algumas sugestões extras não podem ser deixadas de lado. Entre elas, o agendamento da vistoria. Os especialistas sugerem que ela ocorra em um dia em que haja tempo disponível, a fim de que seja feita criteriosamente. Outra recomendação: no caso dos apartamentos que foram personalizados durante a construção, o ideal é que o arquiteto responsável pelas reformas acompanhe a vistoria para verificar se todas as mudanças foram feitas conforme o planejado.
Entrevistado
Advogado Marco Aurélio Luz, presidente da AMSPA (Associação dos Mutuários de São Paulo e Adjacências)
Contatos
contato@amspa.com.br
www.amspavistoria.com.br
www.amspa.com.br
Créditos Fotos: Divulgação/Divulgação/AMSPA
Jornalista responsável: Altair Santos MTB 2330
Fibra de carbono aguarda norma técnica brasileira
Material tem eficiência comprovada no reforço de estruturas de concreto armado, mas seu uso ainda enfrenta resistência no país
Por: Altair Santos
O uso de fibra de carbono para reforçar estruturas de concreto armado não é novidade. O que impressiona é o quanto a tecnologia demorou a chegar ao Brasil. Desenvolvida nos anos 1980, na Suíça, ela levou pelo menos 20 anos para sair dos laboratórios de pesquisa e ganhar o mercado. No entanto, hoje está consolidada nos canteiros de obras europeus e dos Estados Unidos. Por aqui, ainda é usado timidamente. Sobretudo, pela falta de uma norma técnica nacional.
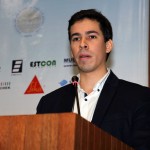
Quando a tecnologia é usada no Brasil, as referências são as normas técnicas norte-americanas (ACI 440 2R:02 (2008)) e o boletim 14XX da fib (Federação Internacional do Concreto). No entanto, a tendência é de que o país em breve tenha sua própria norma técnica. Estimulado pela ABECE (Associação Brasileira de Engenharia e Consultoria Estrutural), foi criado um comitê na ABNT para estudar a criação de uma NBR sobre aplicação de fibra de carbono em estruturas de concreto armado.
No VIII Congresso Brasileiro de Pontes e Estruturas, realizado em maio de 2015, e promovido pela ABECE, a tecnologia esteve entre os temas centrais. O engenheiro civil Gustavo Pérez, graduado pelo ISEP (Instituto Superior de Engenharia do Porto, em Portugal), e consultor técnico da Sika Brasil, palestrou sobre o uso de compósitos de fibra de carbono em recuperação e reforço estrutural do concreto armado.
Segundo o engenheiro, dificilmente o material é usado em fases construtivas ou tem sua utilização prevista em projetos. No entanto, avança em reforços de estruturas. “Sua aplicação não se limita a estruturas de pontes e viadutos, mas a quase tudo que se refere a estruturas de concreto armado, como pilares, lajes e pisos de edifícios, e até paredes”, explica Gustavo Pérez.
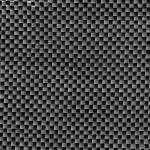
Mitos
O engenheiro comenta que no Brasil ainda existe o conceito de que compósitos de fibra de carbono só podem ser usados em reforços de pontes e viadutos. Seu trabalho no país é para desmistificar isso. “Falta divulgação técnica deste assunto, ainda que a comunidade de projetistas interessados no assunto esteja crescendo”, diz. Para Gustavo Pérez, a criação de uma norma técnica nacional tende a impulsionar a tecnologia. “Ainda que as normas técnicas internacionais sirvam de referência, há particularidades entre um ambiente e outro que só uma norma do próprio país ajuda a resolver”, afirma.
Um dos falsos mitos que uma NBR ajudaria a eliminar é o de que compósitos de fibra de carbono são suscetíveis às condições climáticas, principalmente à incidência dos raios solares. “A fibra de carbono é uma matéria inerte. Portanto, indiferente às condições climáticas. O que pode ser suscetível é o epóxi que vai aderir à fibra. Se ele não for de boa qualidade, pode responder negativamente ao calor ou à umidade. Mas a fibra de carbono, em si, não é afetada por fenômenos meteorológicos. É mais um mito que precisamos combater”, ressalta.
Entrevistado
Engenheiro civil Gustavo Pérez, especialista que trabalha na área de reforço estrutural de concreto armado com compósitos de fibra de carbono. Atua pela Sika Brasil, como consultor técnico.
Contatos
perez.gustavo@br.sika.com
abece@abece.com.br
Créditos Fotos: Divulgação/ABECE/Divulgação
Jornalista responsável: Altair Santos MTB 2330
Porsche, a exemplo da Ferrari, vira grife imobiliária
Sofisticada marca alemã de automóveis projeta construção da Porsche Tower, um edifício de luxo de 57 pavimentos e custo de US$ 560 milhões
Por: Altair Santos
A sofisticada marca de automóveis Porsche está migrando para o mercado imobiliário, como já fez a Ferrari. Projetada pela Porsche Design Group, está em construção na Flórida-EUA, a Porsche Tower. O prédio com 57 pavimentos terá como inovação o elevador-garagem. O morador embarca em seu carro no equipamento, e o veículo é levado até a garagem acoplada ao apartamento. O cronograma prevê que o empreendimento fique pronto em 2017, ao custo de US$ 560 milhões (cerca de R$ 2,240 bilhões). Ainda na etapa das fundações, o edifício já tem metade das unidades negociadas.
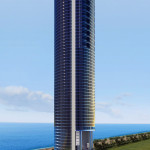
Um detalhe: os futuros moradores estão comprando à vista as unidades, o que já levou ao caixa da construtora a quantia de US$ 200 milhões (aproximadamente R$ 800 milhões). Isso estimula o cumprimento rigoroso do cronograma da obra. Localizado na Sunny Isles Beach, na região de Miami, a Porsche Tower terá formato cilíndrico e seu projeto prioriza sistemas construtivos mistos (concreto e aço), além de investir maciçamente na fachada em vidro. A previsão é que o empreendimento consumirá 12 mil m³ de concreto e duas mil toneladas de aço.
O edifício, que é 100% residencial, tem unidades com as seguintes medidas: 392,9 m² (315,7 m² de área útil), 428,3 m² (258,1 m² de área útil), 496 m² (313 m² de área útil) e 2.253,9 m² (área útil de 1.570 m²). Todas, obviamente, acompanhadas de muito luxo e serviços personalizados. Há opções com quatro ou oito quartos, seis ou dez banheiros, uma ou duas piscinas, terraço com varanda gourmet e garagem para quatro ou nove carros. “Estamos construindo ambientes exclusivos, personalizados, materializando sonhos. A modéstia não tem espaço no Porsche Tower”, confessa Juergen Gessler, CEO da Porsche Design Group.
O empreendimento da Porsche em Miami materializou-se através do investidor Gil Dezer, um dos principais nomes do mercado imobiliário de Miami. Sócio do multimilionário Donald Trump, Dezer constrói no sul da Flórida, paralelamente à Porsche Tower, um complexo de resorts com a marca Trump. São condomínios residenciais, hotéis, prédios habitacionais, prédios comerciais e shopping centers que estão mudando a cara da região, principalmente do balneário Sunny Isles Beach.
Gil Dezer destaca que a grande inovação tecnológica da Porsche Tower está nos elevadores. “Eles irão do andar mais alto até o térreo em um minuto e quinze segundos. É a mais moderna tecnologia em termos de elevadores. Acredito que a partir da Porsche Tower estaremos desenvolvendo um novo conceito de moradias de luxo. Queremos uma casa do futuro, definitivamente”, anuncia.
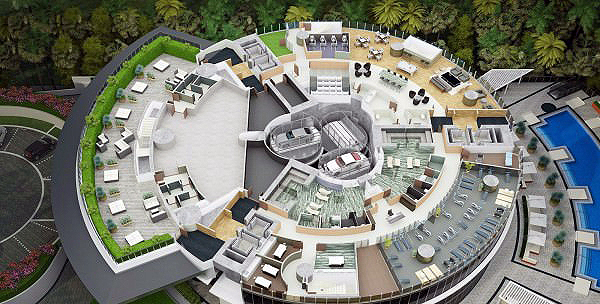
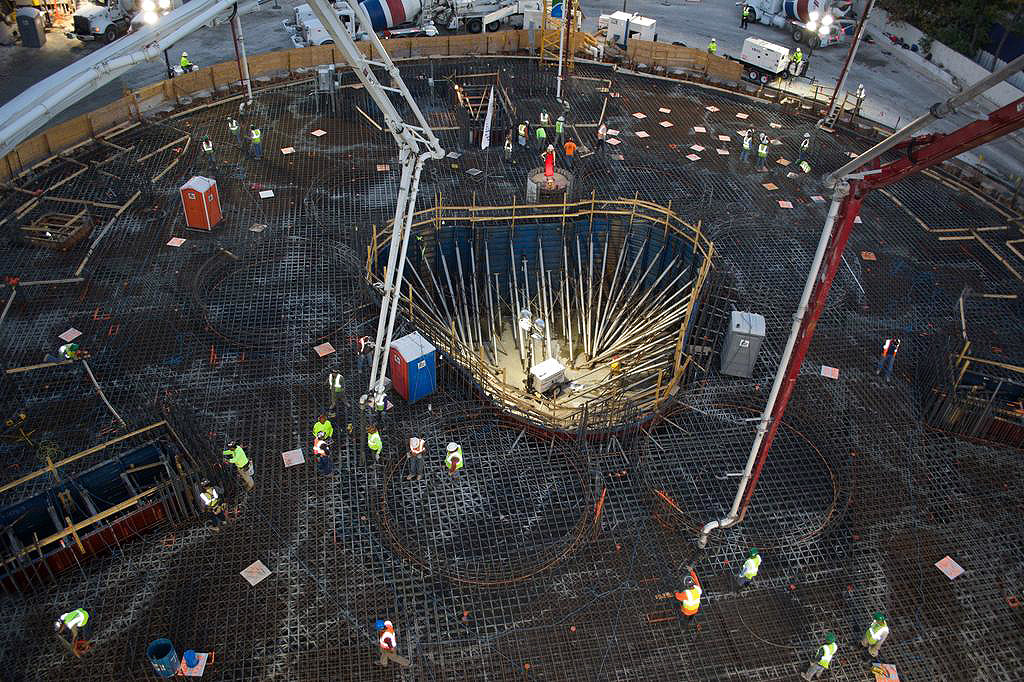
Entrevistado
Porsche Design Group (via assessoria de imprensa)
Contato: contact@porsche-design.com
Créditos Fotos: Divulgação
Jornalista responsável: Altair Santos MTB 2330
Para artefato de cimento, inovar é fazer bem-feito
Em vez de buscar tecnologias e novos equipamentos, fabricantes devem priorizar insumos de qualidade, normas técnicas e desempenho
Por: Altair Santos
O que os fabricantes de artefatos de cimento devem priorizar diante do atual cenário do mercado brasileiro? Buscar tecnologias para se diferenciar, investir em equipamentos que prometem aumentar a produtividade ou concentrar na melhoria do processo de fabricação? O consultor na área de alvenaria estrutural, Davidson Deana, está convicto de que o momento é de aprimorar o produto, recorrendo à qualificação dos insumos e às normas técnicas. “No momento, inovar é fazer bem-feito”, disse, durante palestra no Concrete Congress – evento paralelo ao 9º Concrete Show, ocorrido na cidade de São Paulo entre 26 e 28 de agosto.
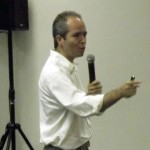
Davidson Deana palestrou no seminário “Segmento de Artefatos no Brasil”, promovido pela ABCP (Associação Brasileira de Cimento Portland). “Muitas vezes, inovação é melhorar a qualidade do concreto, que é o principal insumo de quem fabrica artefatos. Para isso, promover verificações no processo industrial é mais interessante do que sair comprando desesperadamente novas tecnologias e novos equipamentos. Não pode haver a angústia de adquirir uma máquina, achando que ela será a solução de todos os problemas. A preocupação deve ser em fornecer um bom produto usando os recursos de que dispomos”, ensina.
Em sua palestra, Davidson Deana deixou claro que a inovação tem várias faces. “Buscar bons fornecedores e saber negociar preços também é uma postura inovadora. Perseguir normas técnicas, respeitar o meio ambiente, usar matéria-prima de qualidade e garantir desempenho dos produtos também é inovação. Reciclar os processos industriais também é um procedimento inovador. Vale aquela máxima bíblica: conhece a ti mesmo. Minha fábrica de artefatos usa bons agregados? Eu separo e protejo meus insumos das variações climáticas? Eu faço o controle de granulometria e promovo ensaios dos meus artefatos? Tudo isso é inovação”, garante.
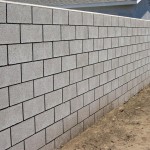
Case e questionamentos
O engenheiro civil citou um case que ele acompanhou no interior de Minas Gerais. “O empresário estava para fechar seu negócio de artefatos de cimento. Então, decidiu investir em qualidade. De que forma? Listou 40 itens de verificação para melhorar seu processo de produção. Além disso, reformou seu maquinário velho, sem comprar nada novo, e passou a aplicar verificações diárias, semanais, mensais e trimestrais. Em seis meses, ele virou o jogo e passou a ganhar mercado na região. Agora, com fôlego para investir, iniciou um novo processo de qualificação de seu negócio. Passou a estudar geologia para entender os agregados que usa em seus produtos e vai investir em um laboratório para ensaiar seus produtos, ou seja, inovou com os recursos de que dispunha”, afirma.
Por fim, Davidson Deana fez uma provocação ao público que assistia a sua palestra - formada basicamente por fabricantes de artefatos que possuem o selo de qualidade da ABCP. “Vendemos produtos ou soluções? Vendemos blocos de concreto ou paredes de vedação e paredes estruturais confiáveis? Vendemos pavers ou calçadas e pavimentos que ajudam as cidades a cumprir as demandas de mobilidade urbana?”, questionou, arrancando aplausos.
Entrevistado
Engenheiro civil Davidson Figueiredo Deana, pesquisador na área de tecnologia do concreto e meio ambiente e sócio da Ethos Soluções
Contato: dfdeana@yahoo.com
Créditos fotos: Divulgação/Cia. Cimento Itambé
Jornalista responsável: Altair Santos MTB 2330
Pré-fabricado avança em obras de infraestrutura
Consolidada em shopping centers, centros de logística e arenas esportivas, industrialização agora busca rodovias, ferrovias e aeroportos
Por: Altair Santos
A construção industrializada já domina setores como o de shopping centers, centros de logística e de arenas esportivas – as obras para a Copa do Mundo de 2014 e para as Olimpíadas de 2016 estão aí para comprovar. Também avança no segmento habitacional. Porém, há uma nova fronteira em que pretende se consolidar: a infraestrutura rodoviária, ferroviária, aeroportuária e de mobilidade urbana. Para isso, ela aprimora ainda mais seus procedimentos de qualidade, tanto para pré-fabricados quanto para pré-moldados.
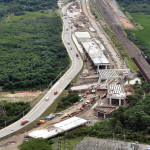
Segundo a presidente-executiva da Abcic (Associação Brasileira da Construção Industrializada do Concreto), Íria Doniak, para atingir o nível de excelência que as obras de infraestrutura exigem, a construção industrializada persegue os 5M: Mão de obra qualificada, Métodos acreditados, Meio ambiente como prioridade, Máquinas com alta tecnologia e Materiais de qualidade. Some-se a isso o respeito irrestrito às sete normas técnicas com que está diretamente relacionada:
- ABNT NBR 9062:2006 – Projeto e execução de estruturas de concreto pré-moldado – Procedimento (em revisão e consulta nacional)
- ABNT NBR 6118:2014 – Projeto de estruturas de concreto – Procedimentos
- ABNT NBR 12655:2006 – Concreto – Preparo, controle e recebimento – Procedimento
- ABNT NBR 14931:2003 – Execução de estruturas de concreto – Procedimentos
- ABNT NBR 14861:2011 - Lajes Alveolares pré-moldadas de concreto protendido (norma entrará em consulta nacional ainda em 2015)
- ABNT NBR 15146:2011 - Controle Tecnológico do Concreto - Qualificação de Pessoal (parte 3)
- ABNT NBR 16258:2014 - Estacas pré-fabricadas de Concreto
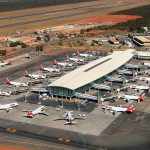
A dirigente da Abcic palestrou no seminário “Infraestrutura em concreto: aplicações inovadoras e desafiadoras”, apresentado no Concrete Congress – evento paralelo ao 9º Concrete Show, que aconteceu na cidade de São Paulo de 26 a 28 de agosto. Segundo ela, independentemente do modelo adotado, se pré-fabricado ou pré-moldado, as peças empregadas em obras de infraestrutura devem perseguir a perfeição. “Por exemplo, para que uma indústria seja considerada como tal deve apresentar no máximo um desvio padrão de 3,5 MPa para concretos fluídos e 4,0 MPa para concretos de abatimentos baixos ”, diz.
Com base neste padrão de qualidade, e nas consequências que ele gera, como redução de custos de manutenção e durabilidade diferenciada, a construção industrializada foi a escolhida, por exemplo, para viabilizar a ampliação do aeroporto de Brasília. A obra envolveu uma área construída de 50.405 m² e volume de concreto na ordem de 7.318 m³. Também foi a opção que viabilizou o terminal de ônibus São Gabriel, em Belo Horizonte - MG, além do complexo viário do Porto de Itaguaí, no Rio de Janeiro, e da estação Pinheiros da linha 4 do metrô paulistano.
Em todos os casos, Íria Doniak lembra que planejamento na construção industrializada é essencial. “Não dá para deixar que as definições ocorram no canteiro de obras. Canteiro é para montagem. O papel da indústria de pré-fabricados é fornecer soluções de engenharia que permitam a execução dos empreendimentos. Para isso, é preciso analisar a condição do terreno, a logística, enfim, todo o estudo de viabilidade para saber se a obra pode ou não receber a construção industrializada”, alerta.
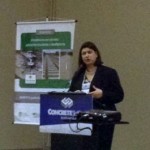
Confira aqui o conteúdo do seminário “Infraestrutura em concreto: aplicações inovadoras e desafiadoras”.
Entrevistada
Engenheira civil Íria Lícia Oliva Doniak, presidente-executiva da ABCIC (Associação Brasileira da Construção Industrializada do Concreto)
Contato: abcic@abcic.org.br
Créditos fotos: Divulgação/Abcic/Cia. Cimento Itambé
Jornalista responsável: Altair Santos MTB 2330
Minha Casa Minha Vida põe sustentabilidade à prova
Programa habitacional enfrenta dilemas e desafios. Não só do ponto de vista de viabilização de recursos como de incorporação de novas tecnologias
Por: Altair Santos
Produzir em escala industrial, mas com qualidade, é a saída para que o programa Minha Casa Minha Vida (MCMV) compense a escassez de recursos gerada por ajustes fiscais e orçamento deficitário em 2016. Mas como atingir essa meta, se o MCMV, em seis anos, avançou pouco sob o ponto de vista de sistemas construtivos inovadores? A rigor, só as construções com paredes de concreto surgiram como alternativa à alvenaria estrutural, que predomina na maioria das obras desde 2009.
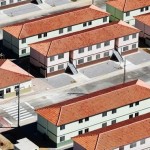
Condomínio do Minha Casa Minha Vida no interior de São Paulo: um dos desafios do programa é aumentar a produtividade sem perder a qualidade
Porém, agora, o Minha Casa Minha Vida não tem como adiar o desafio tecnológico. Principalmente, porque o Ministério das Cidades, que é quem faz a gestão do programa, passa a exigir que todos os projetos do MCMV cumpram a ABNT NBR 15575 – Norma de Desempenho. Em tese, o novo procedimento tende a encarecer o custo das unidades. Mas é aí que reside o principal dilema do Minha Casa Minha Vida: melhorar a qualidade da construção, sem elevar o preço da obra. Pelo contrário, o ideal é que os custos diminuam.
Para construir mais com menos - e com mais qualidade -, construtoras, fabricantes, prefeituras, Cohabs, governos estaduais, centros tecnológicos e universidades foram convocados para criar uma sinergia que permita ao MCMV implantar a Norma de Desempenho 15575 sem perder o foco na habitação de interesse social. Uma solução apontada é compartilhar, via portal do ministério das Cidades, os melhores modelos construtivos regionais.
Por exemplo: supondo que nas regiões sul e sudeste determinada construtora inscrita no MCMV viabilize uma parede de vedação com ótimo desempenho termoacústico, mas a preço competitivo, esse subsistema é submetido a ensaios laboratoriais e, caso aprovado, passa a ser compartilhado como uma construção-referência. Assim, os demais construtores inscritos no programa, e que queiram utilizar o mesmo sistema construtivo, podem copiar o método aplicado na obra.
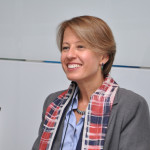
Requisitos mínimos
O objetivo é que os projetos atendam requisitos mínimos, no que diz respeito a critérios como pé direito, paredes internas, segurança, acessibilidade, estanqueidade, durabilidade, sustentabilidade e desempenho termoacústico. É o que ficou claro na recente palestra da arquiteta Maria Salette Weber, coordenadora geral do Programa Brasileiro de Qualidade e Produtividade do Habitat (PBQP-H) – organismo subordinado ao ministério das Cidades.
Ela esteve no seminário “Alvenaria Estrutural do Programa Minha Casa Minha Vida”, que aconteceu no Concrete Congress - evento integrado ao 9º Concrete Show, realizado na cidade de São Paulo de 26 a 28 de agosto. “Todos os materiais e componentes utilizados na construção de moradias populares precisarão atender aos requisitos estabelecidos pela norma. O papel do PBQP-H é justamente auxiliar as construtoras e seus fornecedores a entender como atender estes requisitos”, explica Maria Salette Weber.
A coordenadora do PBQP-H admite, porém, que para atingir essa uniformidade é preciso investir em centros tecnológicos pelo país, a fim de que possam ser realizados os ensaios dos sistemas construtivos. “É preciso fazer um mea culpa por não termos avançado como deveríamos nesta área (oferta de centros tecnológicos), mas o Minha Casa Minha Vida avança no sentido de melhoria das construções. Em 2009, quando foi lançado, o programa tinha duas diretrizes técnicas e agora tem dez. Já os documentos técnicos de avaliação por empresa (DATec), que era um, agora são vinte e um”, afirmou.
Entrevistada
Arquiteta Maria Salette de Carvalho Weber, coordenadora-geral do Programa Brasileiro de Qualidade e Produtividade do Habitat (PBQP_H) da Secretaria Nacional de Habitação do Ministério das Cidades.
Contato: salette.weber@cidades.gov.br
Créditos fotos: Adriana Machado/EBC/Divulgação
Jornalista responsável: Altair Santos MTB 2330
Jundiaí transforma resíduos em praças e calçadas
Cidade do interior de São Paulo assume reciclagem de entulhos da construção civil, transformando-os em agregados para fabricar artefatos de cimento
Por: Altair Santos
Em 2013, a prefeitura de Jundiaí, no interior do estado de São Paulo, se confrontou com grave problema orçamentário: descobriu que apenas 2% de tudo que arrecadava poderia ser destinado aos investimentos, incluindo obras públicas. Porém, as demandas da população, no que se referia à construção de calçadas, pavimentação de ruas, tubulações para saneamento básico e revitalização de espaços públicos, não podiam esperar. Foi aí que surgiu a ideia de transformar resíduos da construção civil (RCC) em dinheiro.
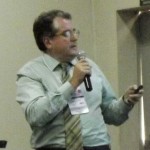
No distrito industrial de Jundiaí foi construído o Geresol (Centro de Gerenciamento de Resíduos Sólidos) - usina mantida pela própria prefeitura, que recebe o RCC, separa os agregados e os utiliza no concreto para produzir peças pré-fabricadas de cimento para fins não estruturais, como pavers, meios-fios e manilhas. Em dois anos, o Geresol já recebeu 700 mil m³ de RCC e extraiu 300 mil toneladas de material reciclado. Isso gerou economia de R$ 13 milhões ao município, que passou a não comprar mais produtos virgens, principalmente areia e brita.
Junto com o Geresol, a prefeitura de Jundiaí implantou um rigoroso sistema de fiscalização do transporte de caçambas e dos geradores de resíduos da construção civil, que passam de 40 mil na cidade. Quanto às empresas que atuam no município, transportando caçambas, elas passam de 250. Os caminhões só podem circular se estiverem cadastrados na prefeitura. Quando isso ocorre, eles passam a ser monitorados por GPS. Para fiscalizar o transporte ilegal, o rastreamento é feito por 25 fiscais.
Brasil só recicla 6% do RCC
O funcionamento do modelo foi apresentado pelo diretor de obra, manutenção e resíduos da Secretaria de Serviços Públicos de Jundiaí, o engenheiro Gilberto Valverde Carneiro, durante a 9ª edição do Concrete Show, que aconteceu de 26 a 28 de agosto na cidade de São Paulo. “Só conseguimos viabilizar o projeto quando mostramos que ele poderia ser superavitário e gerar dinheiro para o município. Essa é a lógica que deve prevalecer para uma política de reaproveitamento de resíduos da construção”, disse, durante o seminário “Resíduos da Construção Civil – Avanços Obtidos nos 13 Anos da Resolução Conama 307”, realizado pelo SindusCon-SP, dentro do Concrete Congress.
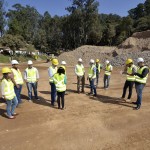
Jundiaí também criou um sistema informatizado chamado CTR (Controle de Transporte de Resíduos). As empresas cadastradas informam onde vão coletar os resíduos, o horário e qual o trajeto a ser percorrido para a descarga no Geresol. O motorista da caçamba também é treinado para orientar o cidadão comum, que contrata a caçamba, a não jogar lixo orgânico ou outros materiais que não sejam entulhos da construção civil. Caso isso ocorra, o contratante da caçamba também está sujeito a receber multa.
O modelo de Jundiaí inspira outros municípios do estado de São Paulo a adotar procedimentos semelhantes. O governo paulista pretende disseminá-lo através de um programa batizado de SIGOR (Sistema de Gerenciamento Online de Resíduos Sólidos). Assis, Catanduva, Santos, São Vicente e Santo André iniciaram tratativas para implantar o programa. Já a prefeitura da cidade de São Paulo também trabalha para implantar um sistema semelhante, enquanto o SindusCon-SP atua paralelamente, prestando orientação técnica e disseminando as práticas de uso de resíduos recicláveis através de um manual criado por especialistas. O objetivo também é sensibilizar outros estados, pois no país apenas 6% dos resíduos da construção civil são coletados, armazenados e reciclados corretamente.
Veja vídeo de como funciona o programa de destinação de RCC em Jundiaí-SP
Baixe aqui o manual “Gestão Ambiental de Resíduos da Construção Civil – Avanços Institucionais e Melhorias Técnicas”.
Entrevistado
Gilberto Valverde Carneiro, graduado em engenharia civil, industrial e de segurança. Atualmente, é diretor de obra, manutenção e resíduos da Secretaria de Serviços Públicos de Jundiaí-SP
Contatos
gcarneiro@jundiai.sp.gov.br
g.valverde@uol.com.br
Créditos fotos: Divulgação/Cia. Cimento Itambé/Prefeitura de Jundiaí/Cleber de Almeida
Jornalista responsável: Altair Santos MTB 2330
Qualidade: palavra-chave na construção (Podcast)
Mercado ainda exige poucos ensaios e testes laboratoriais dos materiais da construção civil, o que atrapalha o setor, alerta Roberto Falcão Bauer
Por: Altair Santos
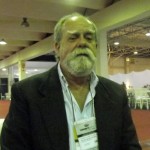
Entrevistado
Roberto José Falcão Bauer é engenheiro civil, com especialidade em patologia de materiais, estruturas e habitabilidade. É professor e diretor-técnico do Centro Tecnológico de Controle da Qualidade Falcão Bauer
Contato
roberto@falcaobauer.com.br
Crédito foto: Divulgação
Jornalista responsável: Altair Santos MTB 2330
Clique no player abaixo e ouça a entrevista na íntegra.